Understanding the Backbone of Modern Manufacturing
The Industrial Automation Software Market represents one of the most significant technological movements reshaping global manufacturing operations today. This specialized software ecosystem serves as the digital nervous system of factories and production facilities, enabling machines to communicate, processes to self-optimize, and operations to run with minimal human intervention. Unlike conventional software applications, industrial automation platforms must meet extremely rigorous requirements for reliability, security, and real-time performance, as even milliseconds of downtime can result in substantial financial losses. According to recent market analyses by Automation World, the industrial automation software sector has consistently outpaced general IT spending growth rates, demonstrating its critical importance to manufacturing competitiveness. For organizations implementing smart factory initiatives, selecting the right automation software infrastructure has become a cornerstone strategic decision with long-term operational implications.
Market Size and Growth Trajectories
The financial scope of the industrial automation software market has reached impressive dimensions, with current valuations exceeding $25 billion globally and projections suggesting a compound annual growth rate (CAGR) of approximately 9.3% through 2030. This remarkable expansion stems from manufacturers’ intensifying need to boost productivity while reducing operational costs in increasingly competitive global markets. North America currently leads market share, followed closely by Europe and the rapidly growing Asia-Pacific region, where countries like China and India are aggressively digitizing their manufacturing sectors. Research from MarketsandMarkets highlights that discrete manufacturing industries—particularly automotive, electronics, and aerospace—represent the largest customer segments, though process industries like chemicals and pharmaceuticals are rapidly accelerating their automation software investments. The market exhibits clear correlation between regional manufacturing output and automation software adoption rates, suggesting digital transformation has become intrinsically linked to industrial competitiveness, similar to how conversational AI has transformed medical office operations.
Key Technology Segments Driving the Market
Within the industrial automation software ecosystem, several technological segments stand out for their growth potential and strategic importance. Manufacturing Execution Systems (MES) continue to serve as the operational cornerstone, providing real-time work order management and production tracking capabilities that bridge planning systems with shop floor automation. Human-Machine Interface (HMI) software has evolved dramatically, incorporating advanced visualization tools, touch interfaces, and mobile accessibility features that resemble consumer applications while maintaining industrial-grade performance. The Supervisory Control and Data Acquisition (SCADA) segment has transitioned from proprietary architectures toward cloud-enabled platforms that facilitate enterprise-wide monitoring. Perhaps most significantly, Industrial Internet of Things (IIoT) platforms have emerged as the fastest-growing category, creating unified environments where operational technology and information technology converge. These platforms, such as PTC ThingWorx, Siemens MindSphere, and GE Digital’s Predix, provide the foundation for building comprehensive digital twins of physical manufacturing assets and processes, creating opportunities for predictive maintenance and process optimization similar to how AI is revolutionizing call centers.
Industry 4.0: The Catalyst for Software Adoption
The ongoing Industry 4.0 revolution has fundamentally altered how manufacturers view automation software investments. No longer considered merely operational tools, these platforms now represent strategic assets in the journey toward fully digitized, connected, and intelligent manufacturing environments. This paradigm shift has accelerated demand for software solutions that enable seamless horizontal integration across departments and vertical integration throughout the production hierarchy. German manufacturers, long considered innovation leaders in this space, were among the first to implement comprehensive Industry 4.0 frameworks, followed by American and Japanese counterparts. Today, even mid-sized manufacturers recognize the competitive necessity of building digital manufacturing capabilities. The World Economic Forum’s Global Lighthouse Network has identified over 100 manufacturing facilities worldwide that exemplify advanced Industry 4.0 implementation, with automation software serving as the central nervous system for these digital transformation success stories. The principles of Industry 4.0 now extend beyond traditional manufacturing into adjacent sectors like logistics and supply chain management, where AI-powered voice agents enable new levels of coordination and efficiency.
AI Integration: Transforming Automation Intelligence
Artificial intelligence has emerged as the defining technological force reshaping industrial automation software platforms. Traditional rule-based automation is rapidly giving way to machine learning models capable of identifying complex patterns in manufacturing data and making autonomous decisions to optimize processes. This evolution is particularly evident in predictive maintenance applications, where AI algorithms analyze equipment sensor data to forecast failures before they occur, dramatically reducing unplanned downtime. In quality control systems, computer vision algorithms paired with high-resolution cameras can detect defects imperceptible to human inspectors at production-line speeds. More sophisticated applications include reinforcement learning systems that continuously optimize process parameters to maximize throughput while minimizing energy consumption and raw material usage. Leading automation vendors like ABB, Siemens, and Rockwell Automation have made substantial investments in AI capabilities, both through internal development and strategic acquisitions of AI startups. These advanced capabilities mirror developments in other industries where AI is transforming phone service capabilities by enabling more natural and effective interactions.
Edge Computing: Processing Where Production Happens
The industrial automation software market has enthusiastically embraced edge computing architectures to address the unique requirements of manufacturing environments. By processing automation data directly on or near production equipment, edge computing overcomes the latency, bandwidth, and reliability limitations of purely cloud-based approaches. This distributed architecture proves particularly valuable for time-sensitive applications like machine safety systems and closed-loop process control, where millisecond response times are essential. Major industrial automation vendors have developed specialized edge hardware platforms optimized for industrial software deployment, including Siemens Industrial Edge, ABB Ability Edge Industrial Gateway, and Rockwell Automation’s Factory Talk Edge. These systems typically feature ruggedized designs, extended temperature ranges, and resistance to electromagnetic interference found in harsh manufacturing environments. The edge computing approach also addresses data sovereignty and security concerns by keeping sensitive production data within facility boundaries while still enabling selective cloud connectivity for analytics and enterprise integration. This balancing of local processing with cloud capabilities creates an ideal foundation for hybrid architectures similar to those used in AI calling business implementations.
Cybersecurity Imperatives in Industrial Environments
The accelerating digitalization of industrial operations has elevated cybersecurity from a peripheral concern to a central requirement in automation software platforms. Unlike conventional IT systems, industrial automation environments present unique security challenges due to their connection to physical production processes where breaches could potentially threaten worker safety, environmental stability, or critical infrastructure. The notorious Stuxnet attack on industrial control systems demonstrated the real-world implications of security vulnerabilities in automation software. In response, the market has witnessed the emergence of specialized industrial cybersecurity solutions that address the particular characteristics of operational technology networks, including the prevalence of legacy systems, extended equipment lifecycles, and proprietary protocols. Standards bodies like the International Society of Automation have developed frameworks specifically for industrial control system security (ISA/IEC 62443), which now guide procurement requirements for automation software. Leading vendors have responded by implementing security-by-design principles, incorporating features like secure boot processes, encrypted communications, role-based access controls, and continuous vulnerability monitoring into their core platforms. These comprehensive security approaches parallel those needed in AI call assistant technologies where sensitive customer information must be carefully protected.
Cloud Manufacturing: The New Operational Paradigm
The concept of cloud manufacturing represents a fundamental reimagining of how production resources are deployed, accessed, and monetized across industrial enterprises. Rather than viewing manufacturing assets as isolated islands of automation, cloud manufacturing platforms treat production capabilities as services that can be dynamically allocated based on changing requirements. Major industrial cloud platforms include Siemens MindSphere, PTC ThingWorx, and GE Digital Predix, all of which provide the infrastructure for building manufacturing applications that span multiple facilities and organizations. These platforms typically offer APIs and development environments that facilitate third-party application creation, fostering industrial software ecosystems that address specific operational challenges. For manufacturers with global operations, cloud manufacturing enables unprecedented visibility across facilities, allowing performance benchmarking, standardization of best practices, and optimization of production workloads across the enterprise network. While early cloud manufacturing implementations focused primarily on monitoring applications, more advanced use cases now include distributed scheduling, remote equipment operation, and virtual commissioning of production systems. The shift toward cloud manufacturing parallels similar trends in other industries where digital platforms enable resource optimization, such as in AI appointment scheduling applications that maximize service efficiency.
Digital Twin Technology: Virtual Representations of Physical Assets
Digital twin technology has rapidly progressed from theoretical concept to practical reality in the industrial automation software landscape. These comprehensive virtual models replicate physical production assets with increasing fidelity, enabling manufacturers to simulate, optimize, and visualize operations in digital environments before implementing changes in the physical world. Leading automation software providers have developed specialized digital twin platforms, including Siemens Tecnomatix, Dassault Systèmes 3DEXPERIENCE, and PTC’s ThingWorx. These systems integrate multiple data sources—3D CAD models, engineering specifications, real-time sensor feeds, and historical performance data—to create living virtual representations of production equipment, production lines, and entire factories. The applications of digital twins range from operator training and maintenance planning to process optimization and virtual commissioning of new production systems. Particularly advanced implementations incorporate physics-based simulations that accurately predict how equipment will respond to different operating conditions, enabling engineers to test process modifications safely in virtual environments. The parallel between digital twins in manufacturing and AI voice conversations is striking—both create faithful representations that enable testing and optimization before real-world implementation.
Robotics Software: Beyond Traditional Industrial Robots
The industrial automation software market has witnessed a remarkable evolution in robotics control platforms, expanding well beyond traditional industrial robot programming to encompass collaborative robots (cobots), autonomous mobile robots (AMRs), and integrated robotic cells. Modern robotics software emphasizes accessibility, with graphical programming interfaces that allow production staff without specialized coding skills to define complex robotic tasks through intuitive flowcharts or demonstration-based teaching. Major robot manufacturers like ABB, KUKA, FANUC, and Universal Robots have developed sophisticated software ecosystems around their hardware platforms, including simulation environments for offline programming and integration with vision systems and other sensors. The market has also seen the emergence of vendor-neutral robotics software platforms like ROS Industrial, which provide standardized frameworks for controlling diverse robot types from multiple manufacturers. These advanced software capabilities have enabled entirely new applications, such as bin-picking systems that use AI vision to identify and manipulate randomly oriented parts—a task previously considered too complex for automation. The focus on intuitive interaction and natural programming parallels developments in conversational AI technology where simplified interfaces make advanced technology more accessible.
Market Leaders and Competitive Landscape
The industrial automation software market features a mix of established industrial giants and innovative technology specialists. Traditional automation powerhouses like Siemens, ABB, Rockwell Automation, Schneider Electric, and Honeywell maintain substantial market shares through their comprehensive portfolios spanning from hardware to advanced software platforms. These companies leverage their deep domain expertise and extensive installed bases to drive software adoption. Meanwhile, specialized software providers like PTC, AVEVA, Dassault Systèmes, and AspenTech have carved out significant positions through focused innovation in specific application domains like product lifecycle management, process simulation, and asset optimization. The competitive landscape continues to evolve through strategic acquisitions, as traditional automation vendors acquire software capabilities while IT giants like Microsoft and Amazon Web Services develop specialized industrial cloud platforms. Regional players maintain strong positions in specific geographies, particularly in high-growth markets like China where domestic automation software providers benefit from national industrial policies. This dynamic market reflects the broader technology landscape where specialized providers (like Bland AI) and established platforms both compete to deliver tailored solutions.
Industry-Specific Automation Software Trends
While industrial automation software shares common technological foundations across sectors, significant industry-specific adaptations have emerged to address unique manufacturing requirements. In the pharmaceutical industry, automation platforms emphasize regulatory compliance capabilities, with specialized functions for electronic batch records, audit trails, and validation procedures that meet FDA 21 CFR Part 11 requirements. Automotive manufacturers have pioneered advanced production tracking systems that enable complete component traceability throughout complex assembly processes, linking individual parts to specific vehicles for quality assurance and recall management. The food and beverage sector utilizes specialized recipe management and batch control systems that ensure product consistency while accommodating natural variations in raw material characteristics. Process industries like chemicals and refining depend heavily on advanced process control (APC) software that maintains optimal operating conditions despite fluctuating input parameters. These industry-specific solutions build upon core automation platforms while incorporating deep domain knowledge accumulated over decades of manufacturing experience. The customization of general-purpose technologies to meet specific industry needs mirrors the approach seen in AI sales solutions where general capabilities are tailored to particular selling contexts.
Low-Code Development Platforms for Industrial Applications
The emergence of low-code and no-code development platforms has democratized industrial application creation, enabling domain experts without traditional programming backgrounds to build sophisticated automation solutions. These platforms provide visual development environments where applications can be assembled from pre-built components using intuitive drag-and-drop interfaces and logical flowcharts. Major automation vendors have introduced their own low-code environments, including Siemens Mendix, Rockwell Automation’s FactoryTalk Innovation Suite, and Schneider Electric’s EcoStruxure Operator Advisor. These tools have proven particularly valuable for creating specialized applications that address facility-specific requirements not covered by commercially available software packages. Common use cases include custom data collection forms, specialized dashboard views, approval workflows, and integrations between disparate systems. By empowering operations personnel to develop their own digital tools, these platforms accelerate solution development while ensuring applications precisely match operational needs. This democratization of development capabilities parallels trends in other business software domains, including AI sales pitch generation where non-technical users can create sophisticated tools without coding expertise.
Supply Chain Integration and Visibility
Modern industrial automation software increasingly extends beyond individual facility boundaries to enable comprehensive supply chain integration. This expanded scope reflects manufacturers’ recognition that optimal performance requires coordinated operation across the entire value chain, from raw material suppliers through distribution channels. Leading automation platforms now provide capabilities for real-time inventory visibility, automated supplier communication, and dynamic production scheduling that responds to changing material availability. Integration with transportation management systems enables just-in-sequence delivery that minimizes inventory while ensuring production continuity. The COVID-19 pandemic accelerated these trends by highlighting the vulnerability of global supply chains to disruption, prompting manufacturers to invest in systems providing greater visibility and adaptability. Advanced implementations incorporate blockchain technology to create immutable records of component origins and handling, particularly valuable in regulated industries with strict traceability requirements. This expansion of automation software’s scope from machines to markets creates unprecedented opportunities for holistic optimization while also increasing the complexity of implementation projects. The integration of diverse business functions resembles the approach of SIP trunking providers who connect disparate communication systems into unified networks.
Subscription Models and Software Licensing Evolution
The industrial automation software market has undergone a fundamental business model transformation, shifting from traditional perpetual licensing toward subscription-based and consumption-based models. This transition mirrors broader software industry trends but faces unique challenges in manufacturing environments where systems often operate for decades and budget allocation typically favors capital expenditures over operational expenses. Leading automation vendors now offer flexible licensing options, including traditional perpetual licenses, term-based subscriptions, and hybrid models that combine baseline capabilities with subscription-based premium features. Some providers have introduced consumption-based pricing for specific capabilities like cloud storage or AI processing, allowing manufacturers to scale costs with actual usage. This evolution creates both opportunities and challenges for manufacturers, who benefit from reduced initial investment but must adjust financial planning to accommodate recurring software costs. For vendors, the subscription model provides more predictable revenue streams while creating stronger incentives for continuous innovation and customer success. The market has also witnessed the emergence of specialized audit and optimization tools that help manufacturers manage increasingly complex software license portfolios. This shift toward service-based delivery models parallels developments in AI reseller opportunities where subscription approaches enable more accessible market entry.
Data Analytics and Operational Intelligence
Advanced analytics capabilities have become central differentiators in the industrial automation software market, with platforms increasingly incorporating sophisticated tools for extracting actionable insights from manufacturing data. These analytics capabilities typically progress through several maturity levels, beginning with descriptive analytics that visualize historical performance, advancing to diagnostic analytics that identify root causes of issues, then to predictive analytics that forecast future conditions, and ultimately to prescriptive analytics that recommend specific actions to optimize outcomes. Leading analytics platforms like GE Digital’s Proficy CSense, Siemens’ Mindsphere Analytics, and ThingWorx Analytics provide pre-built algorithms specifically designed for manufacturing use cases, including anomaly detection, process optimization, and quality prediction. These tools leverage machine learning techniques to identify complex patterns in production data that would be impossible to detect through traditional statistical methods. The most advanced implementations incorporate physics-based models alongside data-driven approaches, combining scientific understanding with empirical learning. For manufacturers, these analytics capabilities transform raw operational data into strategic assets that drive continuous improvement initiatives. This emphasis on converting raw data into actionable intelligence parallels the approach of AI phone number systems that extract meaning and intent from conversations.
Augmented Reality for Industrial Operations
Augmented reality (AR) has emerged as an increasingly important component of industrial automation software strategies, providing intuitive visual interfaces between digital systems and physical production environments. Leading industrial AR platforms include PTC’s Vuforia, Scope AR WorkLink, and TeamViewer Frontline, which enable the overlay of digital information onto real-world equipment through mobile devices, tablets, or dedicated headsets like Microsoft HoloLens. Common AR applications include guided maintenance procedures that visually highlight components requiring attention and provide step-by-step repair instructions directly in the technician’s field of view. Other implementations support operator training, quality inspection, and remote expert assistance, where field personnel can share their visual perspective with remote specialists who then provide guidance through visual annotations. The integration of AR with automation systems creates bidirectional information flow, where AR interfaces not only display data from control systems but also capture operator inputs and observations that feed back into digital records. For manufacturers dealing with skilled worker shortages, AR technology helps transfer knowledge more effectively while reducing training time for new personnel. This visual augmentation of physical reality creates intuitive interfaces between humans and complex systems, similar to how AI voice assistants create natural interfaces between people and digital services.
Regulatory Compliance and Validation Requirements
For manufacturers in regulated industries, automation software must address increasingly complex compliance requirements spanning multiple jurisdictions. Pharmaceutical manufacturers must comply with FDA 21 CFR Part 11 for electronic records and signatures, EU GMP Annex 11 for computerized systems, and similar regulations in other markets. Food producers face FSMA (Food Safety Modernization Act) requirements in the US and equivalent standards globally. Energy producers and utilities must meet NERC CIP (North American Electric Reliability Corporation Critical Infrastructure Protection) standards for operational systems. Leading automation software platforms address these requirements through comprehensive validation features, including audit trails that record all system changes, electronic signature capabilities with multi-factor authentication, data integrity protections, and extensive documentation tools. Specialized validation packages help customers establish and maintain compliance while reducing the burden of regular audits. For many manufacturers, these compliance capabilities represent non-negotiable requirements when selecting automation platforms, as regulatory violations can result in production shutdowns, product recalls, and significant financial penalties. This focus on maintaining regulatory compliance while enabling innovation parallels challenges in other regulated industries where AI call center implementations must balance cutting-edge capabilities with strict compliance requirements.
Open Standards and Interoperability Initiatives
The industrial automation software market has witnessed growing momentum toward open standards and interoperability frameworks that reduce integration complexity and vendor lock-in concerns. Industry consortia like the OPC Foundation have developed widely adopted standards such as OPC UA (Unified Architecture) that provide secure, reliable communication between diverse industrial systems regardless of manufacturer. Other significant standards include ISA-95 for enterprise-control system integration, MQTT for lightweight IoT messaging, and AutomationML for data exchange in engineering workflows. Recent initiatives like the Open Process Automation Forum aim to create fully open, standards-based automation architectures that allow manufacturers to mix components from multiple vendors while maintaining system integrity. Cloud providers have contributed to standardization through efforts like Microsoft’s Open Manufacturing Platform and AWS’s Industrial Software Competency Program. These standards reduce implementation costs while increasing system flexibility, allowing manufacturers to select best-of-breed components rather than committing to single-vendor ecosystems. For automation software vendors, standards compliance has become a competitive necessity rather than an optional feature. This emphasis on interoperability and open integration mirrors the approach of modern voice AI platforms that support flexible integration with diverse business systems.
Implementation Challenges and Success Factors
Despite its tremendous potential, industrial automation software implementation continues to present significant challenges for manufacturers. Success rates vary dramatically across projects, with research from organizations like the Manufacturing Enterprise Solutions Association (MESA) indicating that over 60% of manufacturing software implementations exceed budgeted costs or timelines, while approximately 30% fail to deliver their expected benefits. Common obstacles include insufficient preparation of legacy data sources, inadequate consideration of existing workflows, resistance to process changes from operational staff, and underestimation of integration complexity with existing systems. Organizations that achieve successful implementations typically share several characteristics: clear executive sponsorship, well-defined success metrics established before project initiation, cross-functional implementation teams that combine IT and operational technology expertise, phased deployment approaches with defined value milestones, and comprehensive change management programs that address both technical and human factors. Leading system integrators like Accenture, Capgemini, and specialized industrial automation consultancies play crucial roles in bridging knowledge gaps and transferring implementation best practices. The correlation between implementation approach and project success mirrors findings in other technology domains, including conversational AI implementations where thoughtful deployment strategies significantly impact results.
Future Directions: Quantum Computing and Advanced Simulation
Looking beyond current technological frontiers, quantum computing represents the next transformative force poised to reshape industrial automation software capabilities. While still in early developmental stages, quantum computing promises to solve complex optimization problems that remain intractable for classical computing approaches. Leading industrial automation providers including Siemens, Honeywell, and IBM have established quantum computing research initiatives focused on manufacturing applications. Potential use cases include molecular-level material simulations for product development, complex supply chain optimizations involving millions of variables, and advanced process optimizations that consider vastly more parameters than current systems can process. Complementing quantum advances, neuromorphic computing systems that mimic human brain structures offer promising approaches for handling the massive sensor data streams generated in smart factory environments. These future computing paradigms will likely be integrated first as specialized components within broader automation platforms, handling specific computational tasks while conventional systems manage routine operations. For forward-thinking manufacturers, understanding these emerging technologies has become important for long-term planning, as current automation architecture decisions may either enable or constrain future capabilities. This focus on preparing for next-generation technologies resembles the approach of future-oriented AI businesses that position themselves for emerging opportunities.
Revolutionize Your Operations with Intelligent Automation Solutions
If you’re looking to transform your business operations with cutting-edge technology, Callin.io offers an ideal entry point into the world of intelligent automation. Our platform enables you to implement AI-powered phone agents that can autonomously handle incoming and outgoing calls, mirroring the efficiency gains that industrial automation software delivers in manufacturing environments. These intelligent agents can schedule appointments, answer frequently asked questions, and even close sales opportunities through natural, human-like conversations with your customers.
Callin.io’s free account provides an intuitive interface for configuring your AI agent, with test calls included and a comprehensive task dashboard for monitoring interactions. For businesses requiring advanced capabilities like Google Calendar integration and CRM connectivity, our premium subscription plans start at just 30USD monthly. By automating routine communication tasks, you can free your team to focus on higher-value activities while maintaining consistent customer service quality—achieving the same productivity benefits that manufacturers realize through industrial automation software. Discover more about Callin.io and start your automation journey today.
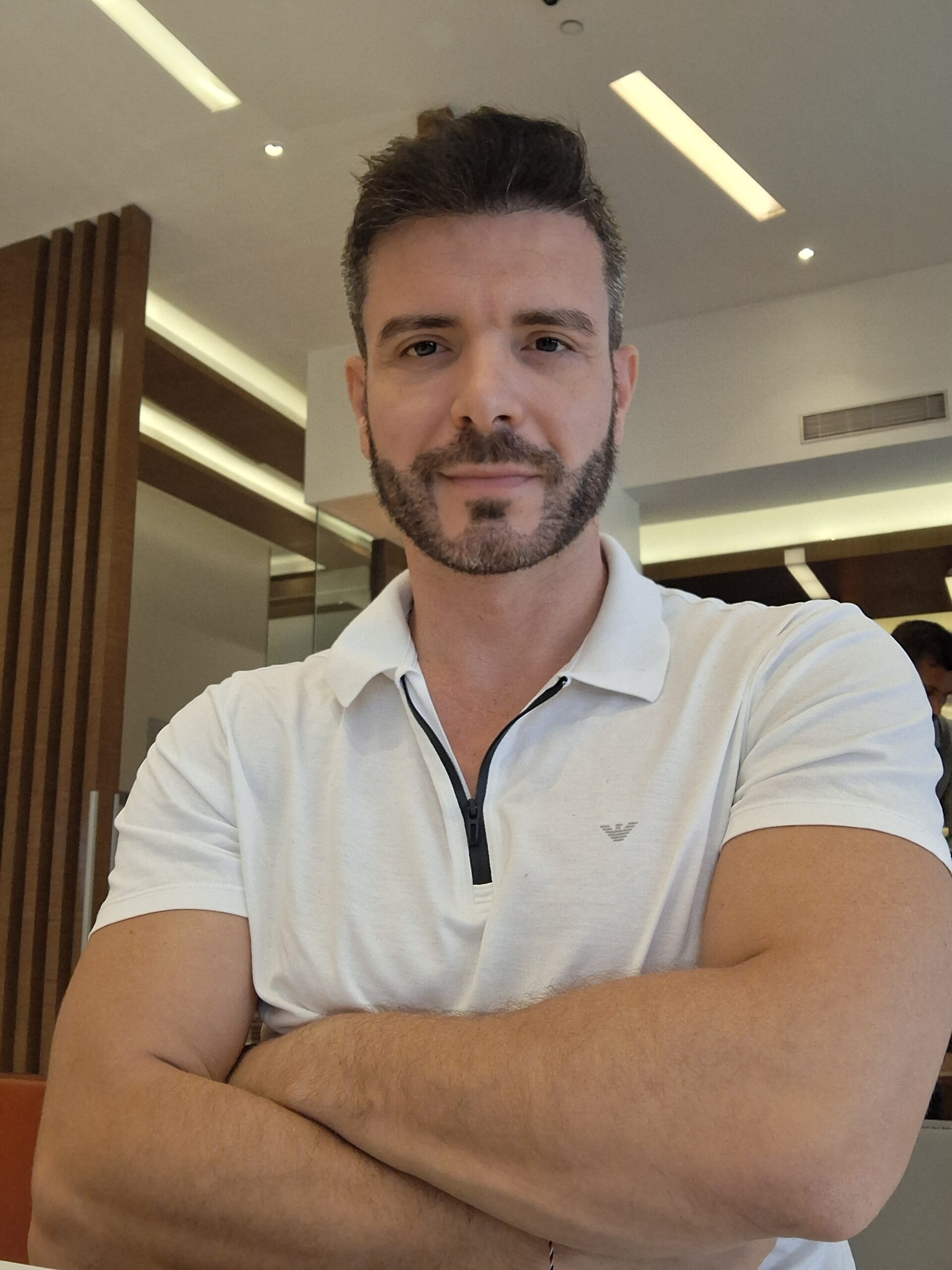
Helping businesses grow faster with AI. 🚀 At Callin.io, we make it easy for companies close more deals, engage customers more effectively, and scale their growth with smart AI voice assistants. Ready to transform your business with AI? 📅 Let’s talk!
Vincenzo Piccolo
Chief Executive Officer and Co Founder