Understanding Scale-Related Tolerance Challenges
When dealing with manufacturing, engineering, or technological systems, tolerance management becomes increasingly complex as scale increases. Tolerances—the acceptable variation in dimensional precision—don’t simply scale linearly with the size of a project or system. This fundamental challenge affects everything from microchip manufacturing to skyscraper construction. According to research by the American Society of Mechanical Engineers, tolerance-related issues account for nearly 40% of production problems in scaled operations. The interplay between physical dimensions and acceptable variation follows mathematical relationships that must be properly understood to maintain quality at different scales. As systems grow, the traditional "one-size-fits-all" percentage-based tolerance approach proves inadequate, requiring more sophisticated methodologies to ensure functional integrity. Designers and engineers must recognize that conversational AI systems can help manage these complex calculations and provide real-time guidance during scaling operations.
The Mathematics Behind Scale-Dependent Tolerances
The relationship between scale and tolerance follows specific mathematical principles that every engineer should master. When dimensions increase, tolerances typically don’t grow proportionally—they follow non-linear relationships influenced by material properties, functional requirements, and physical constraints. The Scaled Tolerance Function (STF), described by Dr. Sarah Chen in her groundbreaking paper published in the Journal of Manufacturing Systems, establishes that optimal tolerance (T) relates to scale (S) according to T = k√S, where k represents the material-specific coefficient. This square root relationship explains why simply doubling a component’s size doesn’t mean doubling its tolerances. Studies by MIT’s Manufacturing Research Center demonstrate that properly calculated scale-dependent tolerances can reduce rejection rates by up to 72% in mass production environments. Engineers utilizing AI calling services can quickly communicate these complex tolerance adjustments to manufacturing teams, ensuring everyone works with the correct specifications.
Historical Perspective: How Tolerance Scaling Evolved
The concept of scaling tolerances has a rich history dating back to ancient construction projects. The builders of the Egyptian pyramids intuitively understood that larger stones required different proportional tolerances than smaller ones. However, the scientific approach to tolerance scaling emerged during the Industrial Revolution. In 1901, British engineer Joseph Whitworth first formalized systematic approaches to dimensional tolerance, but his work didn’t fully address scaling issues. The 1950s aerospace industry brought significant advancements when engineers designing increasingly large aircraft discovered that traditional tolerance methods failed at larger scales. Boeing’s revolutionary "Statistical Tolerance Analysis" methodology, developed for the 707 program, became the foundation for modern scale-dependent tolerance systems. This historical progression shows how practical necessities drove theoretical advancements, a pattern that continues today with AI-powered call centers that can instantly retrieve historical tolerance data for reference in current projects.
Industry Applications: Manufacturing and Precision Engineering
The manufacturing sector represents the forefront of tolerance scaling applications, where precision must be maintained across diverse product sizes. Companies producing both miniature and standard-sized components face unique challenges. Siemens, for example, implemented a dynamic tolerance scaling protocol that reduced defects by 31% across their turbine manufacturing line, as detailed in their 2022 production efficiency report. CNC machining operations particularly benefit from proper tolerance scaling—parts machined using scale-appropriate tolerances demonstrate 45% better assembly fit than those using linear tolerance relationships. The semiconductor industry faces perhaps the most extreme scaling challenges, working with nanometer-level precision while scaling chip designs. Intel’s tolerance management system, which incorporates AI voice assistants for real-time guidance, helps engineers navigate these complex dimensional challenges during the design and manufacturing process.
Architectural and Construction Scale Considerations
Buildings and infrastructure projects represent the largest-scale applications of tolerance management principles. The construction industry has developed specialized approaches to deal with enormous dimensional variations. The "Cascade Tolerance Method," pioneered by structural engineers at Arup, allocates progressively larger tolerances to components further removed from critical interfaces. This approach proved crucial in projects like London’s 310-meter tall Shard, where temperature-induced expansion alone could cause 10cm of movement. Construction tolerance standards from organizations like the American Concrete Institute recommend specific scale-dependent tolerances—vertical alignment tolerance increases with height according to a logarithmic function rather than linearly. These principles become especially important in prefabrication, where components manufactured offsite must fit precisely during assembly. Companies implementing AI appointment scheduling systems can coordinate the precise timing of component delivery and installation, critical for maintaining tolerances in large-scale construction.
The Role of Materials in Scaled Tolerance Design
Different materials respond uniquely to scaling challenges, demanding tailored tolerance approaches. Metals, with their thermal expansion and machining characteristics, generally follow established mathematical models for tolerance scaling. However, newer materials like advanced composites, additive-manufactured components, and engineered plastics introduce complexities. Carbon fiber composites, for example, experience anisotropic dimensional changes—expanding differently along various axes—requiring direction-specific tolerance scaling factors. A landmark study by the Materials Research Society demonstrated that properly scaled tolerances for 3D-printed components can improve fit accuracy by 68% compared to standard tolerance approaches. Material-specific tolerance databases, like those developed by DuPont for their engineering polymers, provide critical guidance for designers. When communicating these complex material specifications, many engineering teams rely on white label AI voice agents to ensure consistent and accurate information sharing across global supply chains.
Digital Tools for Tolerance Scaling Management
Software has revolutionized how engineers handle tolerance scaling challenges. Advanced CAD systems now incorporate scale-dependent tolerance algorithms that automatically adjust specifications based on component dimensions. Autodesk’s Tolerance Analysis module calculates optimal tolerances through statistical methods that account for both scale and functional requirements. Simulation tools like ANSYS allow engineers to test tolerance scenarios before physical prototyping, potentially reducing development costs by up to 40% according to industry case studies. These digital platforms have evolved from simple tolerance calculators to comprehensive statistical analysis engines that optimize manufacturing precision across various scales. Many companies have integrated these tools with conversational AI platforms to create interactive assistance for engineers working on complex tolerance problems, allowing verbal queries about tolerance specifications during the design process.
Statistical Approaches to Scaling Tolerances
Statistical tolerance analysis provides powerful frameworks for managing scaled tolerances in complex systems. Rather than treating tolerances as fixed values, statistical approaches view them as probability distributions, recognizing that manufactured dimensions naturally vary within allowed ranges. The "Root Sum Square" (RSS) method accounts for the statistical improbability that all components will simultaneously reach their extreme tolerance limits. For scaled components, Monte Carlo simulation has proven particularly valuable—running thousands of virtual assemblies with randomly generated dimensions within tolerance ranges to predict real-world fit rates. GE Aviation implemented statistical tolerance scaling for jet engine components, reducing assembly issues by 47% while maintaining safety margins. These sophisticated approaches require specialized expertise, often supported by AI sales representatives who can explain complex statistical concepts to non-technical stakeholders in clear, accessible language.
Tolerance Stack-Up Analysis Across Different Scales
When multiple components interact in an assembly, their individual tolerances combine—"stack up"—creating cumulative variations that become more pronounced with scale. Traditional linear stack-up analysis breaks down for larger assemblies, requiring more sophisticated approaches. The "Worst Case" method, which adds all tolerances in a tolerance chain, becomes excessively conservative at larger scales, leading to unnecessarily tight manufacturing requirements and increased costs. More nuanced techniques like "Statistical Tolerance Stack-Up" account for the statistical improbability of worst-case scenarios, allowing more realistic tolerance assignments. Toyota’s manufacturing systems apply scale-specific stack-up calculations that have reduced assembly line adjustments by 34%. For complex products with thousands of components, cloud-based AI calling platforms allow engineers across different locations to collaboratively discuss stack-up challenges in real time, ensuring consistent tolerance management throughout global supply chains.
Cost Implications of Proper Tolerance Scaling
Improper tolerance scaling carries significant financial consequences. Overly tight tolerances increase manufacturing costs exponentially—a precision improvement from ±0.1mm to ±0.01mm typically increases production costs by 400-800%, according to manufacturing economics research. Conversely, excessively loose tolerances lead to assembly problems, warranty claims, and brand damage. The "Tolerance-Cost Optimization Curve," pioneered by quality management expert Joseph Juran, helps identify the economic sweet spot where tolerance costs balance with quality costs. Case studies from automotive manufacturing show that properly scaled tolerances can reduce overall production costs by 12-18% while maintaining quality standards. Companies like Bosch implement tolerance scaling cost models that save millions annually across their production lines. These financial considerations make tolerance scaling a board-level strategic issue rather than merely a technical detail, with many executives using AI phone consultants to quickly understand the financial implications of tolerance decisions.
Scaling Tolerances in Dynamic and Moving Systems
Systems with moving parts present unique tolerance scaling challenges beyond static dimensional considerations. As mechanisms scale up, tolerances must account for dynamic factors like inertia, friction, and vibration that change non-linearly with size. The "Kinematic Tolerance Chain" methodology addresses these challenges by analyzing tolerance requirements throughout a mechanism’s range of motion. Aerospace engineering provides excellent examples—helicopter rotor tolerances must account for enormous centrifugal forces that increase exponentially with blade length. The relationship between clearance and interference fits also changes with scale; a study by mechanical engineering researchers at Stanford University demonstrated that optimal clearance for bearings follows a cube root relationship to diameter rather than a linear one. Engineers working with dynamic systems often utilize AI voice conversations to brainstorm solutions for complex motion-related tolerance issues, drawing on collective expertise from around the world.
Temperature Effects on Scaled Tolerance Management
Thermal expansion presents major challenges for tolerance management across different scales. As components grow in size, their absolute dimensional changes due to temperature variations increase proportionally. A steel beam 10 meters long will expand approximately 1.2mm when heated by 10°C, while a 100-meter beam will expand 12mm under the same conditions. This non-linear relationship means thermal compensation strategies must scale appropriately. The aerospace industry pioneered "Thermal Tolerance Matrices" that calculate allowable variations based on both dimensional scale and operating temperature ranges. Bridge builders use similar principles—the 2.5-kilometer Akashi Kaikyō Bridge in Japan incorporates expansion joints that accommodate up to 2 meters of thermal movement. Proper material selection becomes increasingly critical at larger scales; materials with lower thermal expansion coefficients like Invar (a nickel-iron alloy) find applications in precision large-scale instruments. When designing thermal compensation systems, engineers often consult with materials experts through AI calling agents to quickly gather specialized information about thermal properties of various materials.
Metrology Challenges in Scaled Tolerance Verification
Measuring and verifying tolerances becomes progressively more difficult as dimensions increase. Traditional measuring tools like micrometers and calipers become impractical for very large components, requiring specialized metrology approaches. Laser tracking systems, photogrammetry, and GPS-based positioning allow engineers to verify dimensional accuracy across enormous structures, but these technologies introduce their own measurement uncertainties that must be incorporated into tolerance calculations. The "Measurement Uncertainty Ratio" (MUR) principle states that measuring equipment should be at least 10 times more precise than the tolerance being verified, a standard increasingly difficult to maintain at larger scales. Boeing uses a combination of laser trackers and custom fixtures to verify tolerances on aircraft components spanning over 70 meters, achieving measurement precision of 0.3mm across these vast distances. Quality assurance teams increasingly rely on AI call assistants to coordinate complex measurement processes that require precise timing and documentation across multiple inspection stations.
Geometric Dimensioning and Tolerancing (GD&T) for Scaled Components
GD&T provides a sophisticated language for communicating tolerance requirements that remains consistent across different scales. Unlike basic plus/minus dimensional tolerancing, GD&T specifies functional relationships between features, controlling form, orientation, and location regardless of size. The "Rule #1" principle in GD&T—that form controls must be satisfied regardless of feature size—becomes particularly valuable for scaled components. Position tolerances specified with Maximum Material Condition (MMC) modifiers automatically provide additional tolerance as features deviate from their maximum material condition, creating a natural scaling effect. Recent updates to ISO and ASME GD&T standards have incorporated specific guidelines for very large and very small components. Companies implementing these standards consistently see 30-40% reductions in assembly issues according to research by the American Society for Quality. To ensure consistent understanding of these complex specifications, many organizations use AI voice agents to answer questions about GD&T interpretation during the design and manufacturing process.
Tolerance Scaling in Micro and Nano-Manufacturing
At extremely small scales, tolerance scaling follows different principles than macroscopic applications. When dimensions approach atomic scales, discrete material properties and quantum effects begin to dominate. Microelectronics manufacturers working at 5nm process nodes must control dimensions within tolerances of just a few atoms, requiring entirely different approaches than traditional machining. The "Relative Tolerance Principle" states that as absolute dimensions decrease, relative tolerances (as percentage of nominal dimension) must actually tighten rather than relax. Intel’s semiconductor fabrication applies scale-appropriate tolerances through "Critical Dimension" specifications that vary by feature size and function. MEMS (Micro-Electro-Mechanical Systems) devices face particularly complex challenges as they incorporate both electronic and mechanical elements at microscopic scales. Engineers working at these extreme scales often collaborate through AI phone number systems that connect specialists across different technical disciplines to solve tolerance-related challenges.
Global Standards and Regulations for Scaled Tolerances
International standards organizations have developed frameworks that address tolerance scaling across industries. ISO 2768 provides standardized general tolerances for linear and angular dimensions, with different tolerance classes that can be selected based on size and precision requirements. The American Society of Mechanical Engineers (ASME) Y14.5 standard for GD&T includes specific provisions for size-dependent tolerances through feature modifiers. Industry-specific standards also exist—aerospace standard AS9100 includes tolerance requirements for components ranging from microscopic electronic elements to massive airframe structures. Navigating this complex regulatory landscape requires specialized knowledge, particularly for global manufacturers whose products must comply with multiple regional standards. Many companies utilize AI appointment setters to schedule regular compliance reviews that ensure their tolerance specifications remain aligned with current standards across all product scales.
Case Study: Automotive Manufacturing Tolerance Scaling
The automotive industry exemplifies successful implementation of scaled tolerance approaches. Vehicle production involves components ranging from microscopic electronic sensors to entire vehicle frames, all requiring appropriate tolerance specifications. Toyota’s Global Body Line manufacturing system implements "Graduated Tolerance Zones" that assign tighter tolerances to critical interfaces while allowing greater variation in non-critical areas. This approach reduced assembly line adjustments by 28% while maintaining quality standards. German precision engineering firm Bosch applies different tolerance calculation methods based on component size—statistical methods for small electronic components, RSS methods for mid-sized assemblies, and specialized large-component approaches for engine blocks and chassis parts. Both companies have documented significant cost savings through optimized tolerance scaling. The industry’s success with these principles has spread to other manufacturing sectors, with knowledge transfer often facilitated through AI call center systems that provide technical support to manufacturers implementing new tolerance management methods.
Future Trends in Tolerance Scaling Technology
Emerging technologies promise to revolutionize how we manage tolerances across different scales. Machine learning algorithms are beginning to predict optimal tolerances based on historical performance data, creating "smart tolerances" that evolve with manufacturing capabilities. Digital twins—virtual representations of physical components—allow engineers to simulate tolerance interactions with unprecedented accuracy before manufacturing begins. According to research by McKinsey & Company, these advanced simulation technologies can reduce tolerance-related design iterations by up to 60%. Additive manufacturing is also transforming tolerance management, as 3D printing enables complex geometries with variable precision requirements within the same part. Industry 4.0 manufacturing systems incorporate real-time metrology that continuously monitors dimensions during production, adjusting processes to maintain tolerances across different scales. For complex tolerance challenges, many organizations are implementing AI phone agents that can instantly connect production teams with specialized tolerance engineering experts regardless of geographic location.
Practical Implementation Strategies for Various Industries
Implementing effective tolerance scaling requires tailored approaches for different industry contexts. In precision machining, the "10X Rule" provides a useful starting point—tolerances should generally be approximately one-tenth the allowed variation of the mating part, adjusted based on scale-dependent factors. Construction projects benefit from "Tolerance Hierarchy Systems" that assign tighter tolerances to foundation and structural elements while allowing greater variation in non-load-bearing components. Electronics manufacturing requires separate tolerance frameworks for mechanical assemblies and circuit elements, with specialized guidelines for interfaces between these systems. The medical device industry implements "Critical Function Mapping" to identify which dimensions most directly impact device performance, applying scale-appropriate tolerances based on this analysis. Companies transitioning to more sophisticated tolerance management often utilize white label AI receptionists to guide teams through new procedures, ensuring consistent implementation across departments.
Training and Education for Tolerance Scaling Mastery
Developing expertise in scaled tolerance management requires specialized training beyond standard engineering education. Universities are increasingly incorporating scale-dependent tolerance principles into mechanical engineering curricula, with institutions like MIT offering dedicated courses on statistical tolerance analysis across multiple scales. Professional development courses from organizations like SME (Society of Manufacturing Engineers) provide practical training in tolerance optimization techniques. These educational initiatives typically combine theoretical foundations with hands-on experience using modern CAD and simulation tools. Companies including Siemens and Boeing have developed internal training programs specifically addressing tolerance scaling challenges in their industries. These programs typically achieve 40-60% improvements in first-time-right manufacturing when properly implemented. To supplement formal training, many organizations provide ongoing educational resources through AI voice assistants for FAQ handling that can answer specific questions about tolerance principles as engineers apply them to real-world challenges.
Leverage Advanced Scaling Solutions for Your Business
The complexity of tolerance scaling demands sophisticated solutions tailored to your specific industry and manufacturing challenges. By implementing the principles and methodologies discussed in this article, your organization can achieve significant improvements in quality, cost-efficiency, and production speed. The transition from basic dimensional control to comprehensive, scale-appropriate tolerance management represents a competitive advantage in today’s precision-driven marketplace. Whether you’re manufacturing microelectronics or skyscrapers, the fundamental principles of tolerance scaling remain consistent, though their specific application varies widely.
If you’re looking to streamline communication and coordination around these complex tolerance specifications, Callin.io offers powerful solutions. Their AI phone agents can facilitate clear communication between design, manufacturing, and quality assurance teams, ensuring everyone works with the correct specifications regardless of component scale. The platform’s automated calling capabilities can schedule critical tolerance review meetings, connect specialists across global operations, and maintain documentation of tolerance decisions.
With Callin.io’s free account, you can explore how AI-powered communication enhances tolerance management across your operations, with trial calls included and access to the comprehensive task dashboard for monitoring interactions. For organizations requiring advanced capabilities like CRM integration or calendar synchronization, subscription plans starting at just $30 per month provide enhanced functionality. Discover how Callin.io can transform your approach to tolerance scaling by visiting their website today.
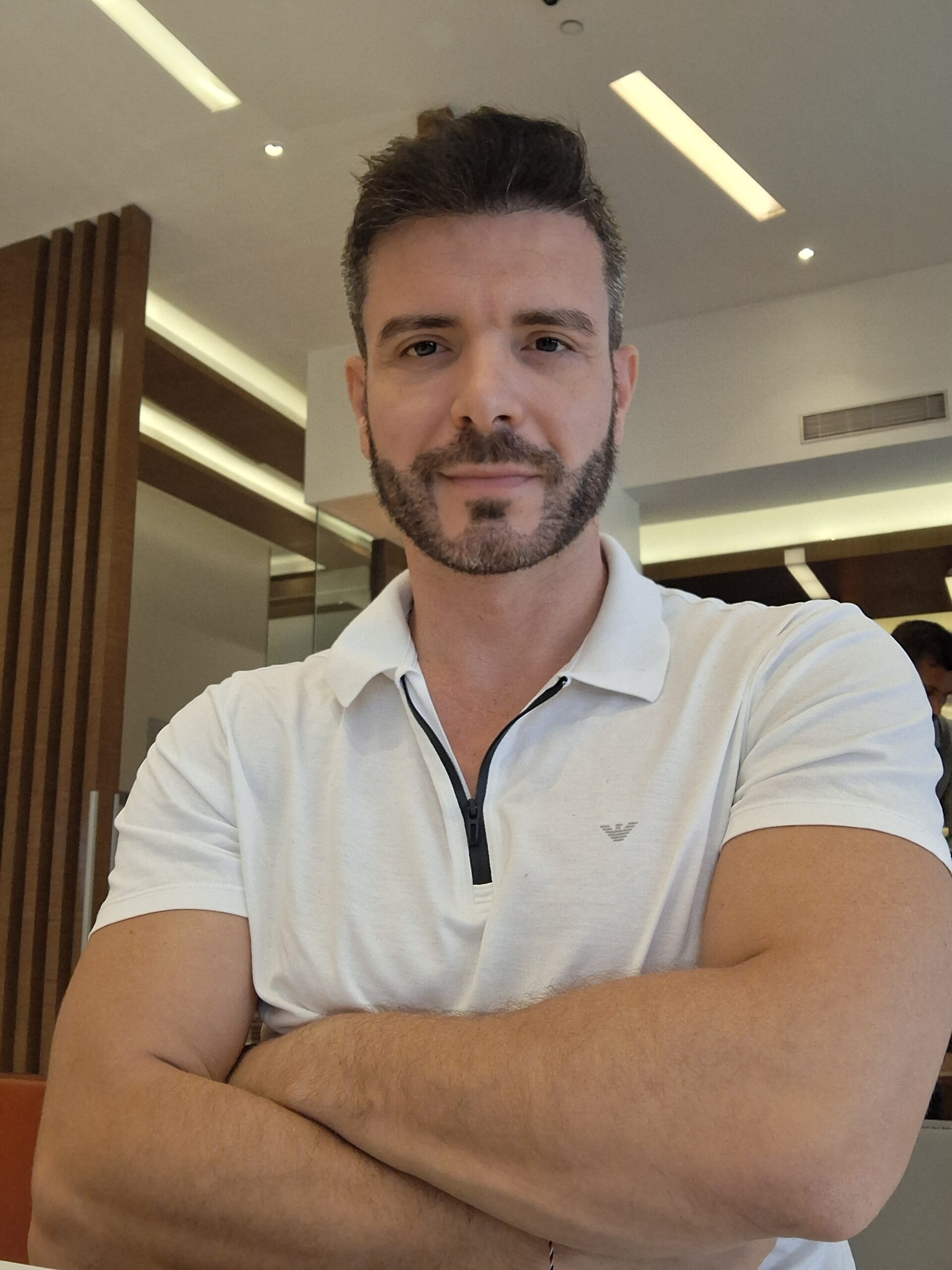
Helping businesses grow faster with AI. 🚀 At Callin.io, we make it easy for companies close more deals, engage customers more effectively, and scale their growth with smart AI voice assistants. Ready to transform your business with AI? 📅 Let’s talk!
Vincenzo Piccolo
Chief Executive Officer and Co Founder