The Transformation of Modern Supply Chains Through Artificial Intelligence
Supply chains have become increasingly complex in today’s business environment, with numerous moving parts spanning multiple countries and stakeholders. AI solutions for supply chain management represent a fundamental shift in how companies coordinate these intricate systems. Rather than just automating existing processes, artificial intelligence technologies are redefining what’s possible by enabling predictive capabilities, autonomous decision-making, and unprecedented visibility across the entire supply network. According to research from McKinsey & Company, organizations implementing AI in their supply chains have seen up to 65% reduction in lost sales and 20-50% reduction in inventory costs. This transformation isn’t just about efficiency—it’s creating entirely new competitive advantages for forward-thinking businesses.
Predictive Analytics: Forecasting with Unprecedented Accuracy
One of the most powerful applications of AI in supply chain management is predictive analytics. Traditional forecasting methods often struggle with the sheer number of variables that impact supply and demand. AI algorithms excel at processing massive datasets from multiple sources—weather patterns, social media trends, economic indicators, historical sales data—to generate remarkably accurate predictions about future needs. For instance, Walmart has implemented AI forecasting that reduces out-of-stock items by 30%, while Amazon’s predictive shipping anticipates orders before customers place them. The real breakthrough isn’t just better numbers, but the ability to continuously learn and improve predictions by analyzing the differences between forecasts and actual results, creating a perpetually self-improving system that grows more valuable over time.
Inventory Management Revolution: The End of Stockouts and Overstocking
AI-powered inventory management represents a quantum leap beyond traditional systems by dynamically balancing the competing priorities of capital efficiency and product availability. Rather than relying on static reorder points, AI solutions continuously evaluate inventory levels against predicted demand, supplier lead times, and even transportation conditions to optimize stocking decisions. A notable example is Ocado, the online grocery retailer, which uses AI to manage over 50,000 SKUs with minimal waste despite the perishable nature of their products. These systems shine particularly in managing seasonal fluctuations and unexpected demand spikes, automatically adjusting ordering patterns to maintain optimal inventory levels while simultaneously reducing the human workload in inventory management functions. The financial impact is substantial—companies using AI for inventory optimization report working capital improvements of 15-30%.
Intelligent Supplier Relationship Management
The complexity of modern supplier networks demands sophisticated approaches to supplier selection, evaluation, and relationship management. AI solutions in supplier management analyze vast datasets to identify the most reliable vendors, predict potential supply disruptions, and even suggest alternative sourcing strategies. For example, Procter & Gamble uses AI to monitor over 200 factors that might indicate supplier risk, from weather events to financial indicators, allowing them to proactively address potential issues before they impact operations. Similarly, AI-powered communication systems can maintain consistent supplier engagement through automated interactions that feel personal while ensuring important information is exchanged efficiently. These technologies also excel at contract analysis, automatically identifying favorable terms, compliance issues, and opportunities for negotiation improvement across thousands of supplier agreements.
Transportation Optimization: Beyond Route Planning
Transportation represents a significant cost center in most supply chains, making it a prime target for AI optimization. Modern AI transportation management systems go far beyond simple route planning, incorporating real-time traffic data, vehicle telemetry, driver behavior, weather conditions, and delivery window commitments to continuously optimize logistics operations. Companies like DHL have implemented AI systems that reduce last-mile delivery costs by up to 15% while simultaneously improving on-time performance. These systems can also predict maintenance needs for vehicles based on operational patterns, preventing costly breakdowns and service disruptions. The environmental impact is equally significant, with AI-optimized transportation networks reducing carbon emissions by 8-10% through more efficient routing and load consolidation, as documented by the World Economic Forum’s research on supply chain sustainability.
Warehouse Automation and Robotics Integration
The marriage of AI with robotics and automation is transforming warehousing operations from labor-intensive bottlenecks into high-speed fulfillment hubs. AI algorithms coordinate robot movements, optimize picking sequences, and dynamically reorganize inventory placement based on predicted demand patterns. Amazon’s fulfillment centers exemplify this approach, with AI systems directing thousands of robots that bring shelves to human pickers—increasing picking rates by 2-3 times while reducing walking distance for workers by up to 80%. Beyond physical robotics, intelligence extends to automated storage and retrieval systems (AS/RS) that maximize space utilization while ensuring items are stored in optimal locations for rapid retrieval. The true power comes from the learning capabilities—these systems continuously improve by analyzing their own performance data, identifying inefficiencies and testing new approaches to warehouse layout and operation.
Demand Sensing: Understanding Customer Needs in Real-Time
Traditional demand forecasting typically relied on historical sales data, leading to significant inaccuracies when market conditions changed. AI-powered demand sensing represents a fundamental shift by incorporating real-time signals from multiple channels—social media sentiment, search trends, competitor pricing, weather forecasts, and even macroeconomic indicators—to provide a continuously updated view of likely customer behavior. Procter & Gamble’s implementation of demand sensing technology reduced forecast error by 40% and improved service levels by 2-5 percentage points across their product portfolio. The most sophisticated systems can detect early signals of demand shifts weeks before they would appear in sales data, giving operations teams precious lead time to adjust production and distribution plans. This capability is particularly valuable for products with short lifecycles or seasonal demand patterns, where historical data quickly loses relevance as consumer preferences evolve.
Supply Chain Risk Management and Resilience
The disruptions caused by recent global events have highlighted the critical importance of supply chain risk management. AI solutions for supply chain resilience continuously monitor thousands of potential risk factors—from geopolitical events to natural disasters, supplier financial health to labor disputes—and assess their potential impact on specific supply chain nodes. These systems can simulate multiple "what-if" scenarios to identify vulnerabilities before they’re exposed by actual events. Cisco’s AI risk management platform monitors over 500 million data points daily across their global supply network, allowing them to proactively mitigate potential disruptions. Beyond just identifying risks, advanced systems automatically generate alternative sourcing plans, inventory positioning strategies, and logistics adjustments to minimize the impact of predicted disruptions. The integration with communication systems ensures that all stakeholders receive timely, relevant information about potential issues and response plans.
Quality Control and Defect Reduction
Quality issues can severely impact supply chain performance through returns, warranty claims, and reputation damage. AI-powered quality control systems analyze production data, supplier quality metrics, and even images from inspection cameras to identify potential quality problems before products leave manufacturing facilities. For example, automotive manufacturers use computer vision systems that can detect subtle defects in painted surfaces that would be invisible to human inspectors. These systems continuously learn from each inspection, becoming increasingly adept at distinguishing between normal variations and actual defects. The predictive capabilities extend to identifying patterns that precede quality issues—such as specific combinations of raw material characteristics, production parameters, and environmental conditions—allowing preemptive adjustments before defects occur. In pharmaceutical supply chains, these systems have reduced quality-related losses by up to 50% while simultaneously improving regulatory compliance.
End-to-End Supply Chain Visibility
Perhaps the most transformative aspect of AI in supply chain management is the creation of comprehensive visibility across previously siloed operations. AI-powered supply chain control towers integrate data from multiple systems—ERP, WMS, TMS, and external partners—to create a single, coherent view of the entire supply network. These platforms don’t just display information; they interpret it, identifying patterns, exceptions, and opportunities that would be impossible for human operators to detect across such complex systems. Unilever’s digital twin of their global supply chain allows them to visualize impacts across more than 100,000 shipping locations in near real-time. The most advanced implementations use natural language processing to allow non-technical users to ask complex questions about supply chain performance and receive immediate, actionable insights without requiring specialized analytical skills or knowledge of the underlying data structures.
Customer-Centric Supply Chain Design
Traditional supply chains were designed primarily for cost efficiency, but AI is enabling organizations to optimize for customer experience without sacrificing financial performance. AI-driven customer-centric supply chains analyze individual customer preferences, purchase history, and service expectations to create personalized fulfillment experiences. Nike’s implementation of this approach allows them to offer customized products with delivery speeds comparable to off-the-shelf items by dynamically adjusting production and distribution based on individual orders. These systems continuously evaluate the trade-offs between service levels and operational costs, making nuanced decisions about inventory placement, transportation modes, and fulfillment methods based on the specific value of each customer relationship. Research from Gartner suggests that companies with customer-centric supply chains achieve revenue growth 2-3% higher than industry averages while maintaining competitive cost structures.
Sustainable Supply Chain Management Through AI
Environmental responsibility has become a critical concern for supply chain managers facing regulatory pressures and consumer expectations for sustainability. AI solutions for sustainable supply chains optimize operations to minimize environmental impact through reduced emissions, waste reduction, and resource conservation. Unilever uses AI to analyze the carbon footprint of thousands of ingredients and packaging materials, automatically suggesting alternatives that maintain product performance while reducing environmental impact. Transportation optimization algorithms incorporate carbon emissions alongside traditional cost metrics, finding the optimal balance between environmental and financial objectives. AI systems also excel at identifying opportunities for circular economy initiatives by analyzing product returns, recycling streams, and remanufacturing possibilities. The measurable impacts are significant—companies implementing these systems report 15-25% reductions in supply chain carbon emissions while simultaneously reducing operational costs.
Collaborative Planning and Execution
Traditional supply chain planning often suffered from information silos and time delays between planning cycles. AI-driven collaborative planning creates a continuous, integrated planning process that spans organizational boundaries and responds dynamically to changing conditions. Algorithms process inputs from multiple stakeholders—suppliers, manufacturers, distributors, retailers—to create aligned plans that optimize for system-wide performance rather than local objectives. P&G’s "Control Tower" platform allows real-time collaboration with retail partners, automatically adjusting production and distribution plans based on point-of-sale data. These systems excel at resolving conflicts between competing priorities, finding compromise solutions that balance service levels, inventory costs, and production efficiency. The impact on planning cycles is dramatic, with companies reporting 70-80% reductions in planning time while simultaneously improving plan quality and stakeholder alignment.
Human-Machine Collaboration in Supply Chain Management
The most successful AI implementations recognize that the goal isn’t to replace human decision-makers but to augment their capabilities. AI-enabled human-machine collaboration creates systems where algorithms handle vast data processing and routine decisions while human experts focus on strategic thinking, relationship management, and creative problem-solving. Conversational AI interfaces allow supply chain professionals to interact naturally with complex systems, receiving insights and recommendations in accessible formats. For example, Maersk’s supply chain managers use an AI assistant that monitors their global shipping network, proactively alerting them to potential issues and suggesting mitigation strategies. The key innovation is creating appropriate trust—these systems explain their reasoning and confidence levels, allowing human operators to understand when and why to override algorithmic recommendations. Organizations that effectively implement this collaborative approach report 20-30% improvements in decision quality and significant increases in employee satisfaction as routine tasks are automated.
AI-Powered Returns Management
Returns management has traditionally been a challenging aspect of supply chain operations, with high processing costs and significant environmental impacts. AI solutions for returns management transform this process by predicting return likelihood at the point of sale, optimizing return logistics, and maximizing recovered value from returned items. Retailers like Zara use algorithms that analyze customer purchase history and product characteristics to identify orders with high return probability, allowing preemptive interventions such as size recommendations or fit guidance. For items that are returned, AI systems determine the optimal disposition path—resell, refurbish, recycle, or dispose—based on item condition, processing costs, and market demand. These technologies have reduced returns processing costs by 15-25% while simultaneously improving the sustainability of returns operations. The integration with customer service systems ensures a positive consumer experience despite the inherent frustrations of the returns process.
Cost-to-Serve Optimization Through AI
Understanding the true profitability of individual customers, products, and channels is essential for strategic supply chain decisions. AI-powered cost-to-serve analysis integrates data from multiple systems to create granular visibility into the actual costs of serving specific market segments. These platforms automatically identify high-cost activities, unprofitable customer relationships, and opportunities for service differentiation based on profitability. For example, a major consumer products company discovered through AI analysis that their premium delivery service was actually less costly for certain customer segments due to larger order sizes and more predictable ordering patterns. The most advanced implementations continuously monitor cost-to-serve metrics against strategic objectives, automatically adjusting service levels and fulfillment methods to optimize profitability while maintaining customer satisfaction. Companies implementing these solutions report margin improvements of 3-5 percentage points through more informed pricing and service level decisions.
Integration of Digital Supply Chain Twins
The concept of digital twins—virtual replicas of physical systems—is being applied to entire supply networks with remarkable results. AI-enabled digital supply chain twins combine real-time operational data with sophisticated simulation capabilities to create living models of supply networks. These digital replicas allow supply chain leaders to test scenarios, evaluate trade-offs, and optimize decisions before implementing them in the physical world. Unilever’s digital twin encompasses over 300 manufacturing facilities and thousands of suppliers, allowing them to simulate the impact of potential disruptions or strategic changes across their entire operation. The predictive capabilities extend to capacity planning, where organizations can evaluate the impact of demand growth on their existing infrastructure to make informed investment decisions. Research from MIT’s Center for Transportation & Logistics indicates that companies using digital twins for supply chain planning reduce implementation risks by 40-60% while identifying optimization opportunities that would be invisible with traditional planning approaches.
Supply Chain Finance Optimization
The financial dimensions of supply chain management often represent significant opportunities for value creation. AI solutions for supply chain finance analyze payment terms, inventory holding costs, and working capital requirements across the extended enterprise to identify optimization opportunities. These systems can automatically match early payment discount opportunities against the organization’s cost of capital, identifying when accelerated payments create financial value. For suppliers with cash flow constraints, AI algorithms determine when supply chain financing offers better terms than traditional financing options. Companies like Siemens have implemented AI platforms that have reduced working capital requirements by hundreds of millions of dollars while simultaneously strengthening supplier relationships through more favorable payment options. The most sophisticated implementations integrate directly with financial systems to execute optimization strategies automatically, adjusting payment timing based on continuous evaluation of financial conditions and business priorities.
Last-Mile Delivery Innovation
The final step in the supply chain—delivering products to end customers—has become increasingly critical in the competitive landscape. AI-driven last-mile optimization addresses this challenge by combining route optimization, dynamic scheduling, and customer preference modeling to create efficient, responsive delivery operations. Companies like DoorDash use AI algorithms that consider dozens of variables—traffic patterns, driver location, order preparation time, customer location—to orchestrate millions of deliveries with minimal waste and maximum customer satisfaction. Predictive models anticipate delivery demand by geographical area and time period, allowing proactive positioning of delivery resources before orders arrive. The integration with customer communication systems ensures transparency throughout the delivery process, with automated updates and accurate arrival time predictions. Organizations implementing these technologies report 20-30% improvements in delivery efficiency alongside significant increases in customer satisfaction scores.
Future Directions: Autonomous Supply Chains
The ultimate vision for many organizations is the development of largely autonomous supply chains that self-optimize based on strategic objectives. Autonomous supply chain systems represent the convergence of multiple AI technologies—machine learning, natural language processing, computer vision, and autonomous robotics—creating operations that require minimal human intervention for routine functions. Early examples include Ocado’s highly automated fulfillment centers, where AI orchestrates robots that pick, pack, and ship grocery orders with minimal human involvement. These systems continuously evaluate their own performance against key metrics, automatically adjusting operational parameters to improve results. While fully autonomous supply chains remain aspirational for most organizations, the components are rapidly maturing, with leading companies implementing increasingly sophisticated automation across specific supply chain functions. Research from Gartner suggests that by 2025, over 25% of large organizations will operate semi-autonomous supply networks that learn, adapt, and recover with minimal human intervention.
Transform Your Supply Chain with AI-Powered Communication
If you’re looking to elevate your supply chain operations with cutting-edge technology, consider exploring Callin.io. This innovative platform allows you to implement AI-powered phone agents that can autonomously handle both inbound and outbound communications throughout your supply chain network. With Callin.io’s sophisticated AI phone agents, you can automate supplier communications, delivery confirmations, inventory alerts, and customer notifications—all while maintaining natural-sounding interactions that strengthen relationships with your supply chain partners.
Setting up your supply chain communication system on Callin.io is straightforward with their user-friendly interface. The free account includes test calls and access to a comprehensive dashboard for monitoring all AI interactions across your supply network. For organizations requiring advanced capabilities such as integration with supply chain management systems and CRM platforms, premium plans start at just $30 per month. Discover how Callin.io can become the communication backbone of your AI-enhanced supply chain by visiting their website today.
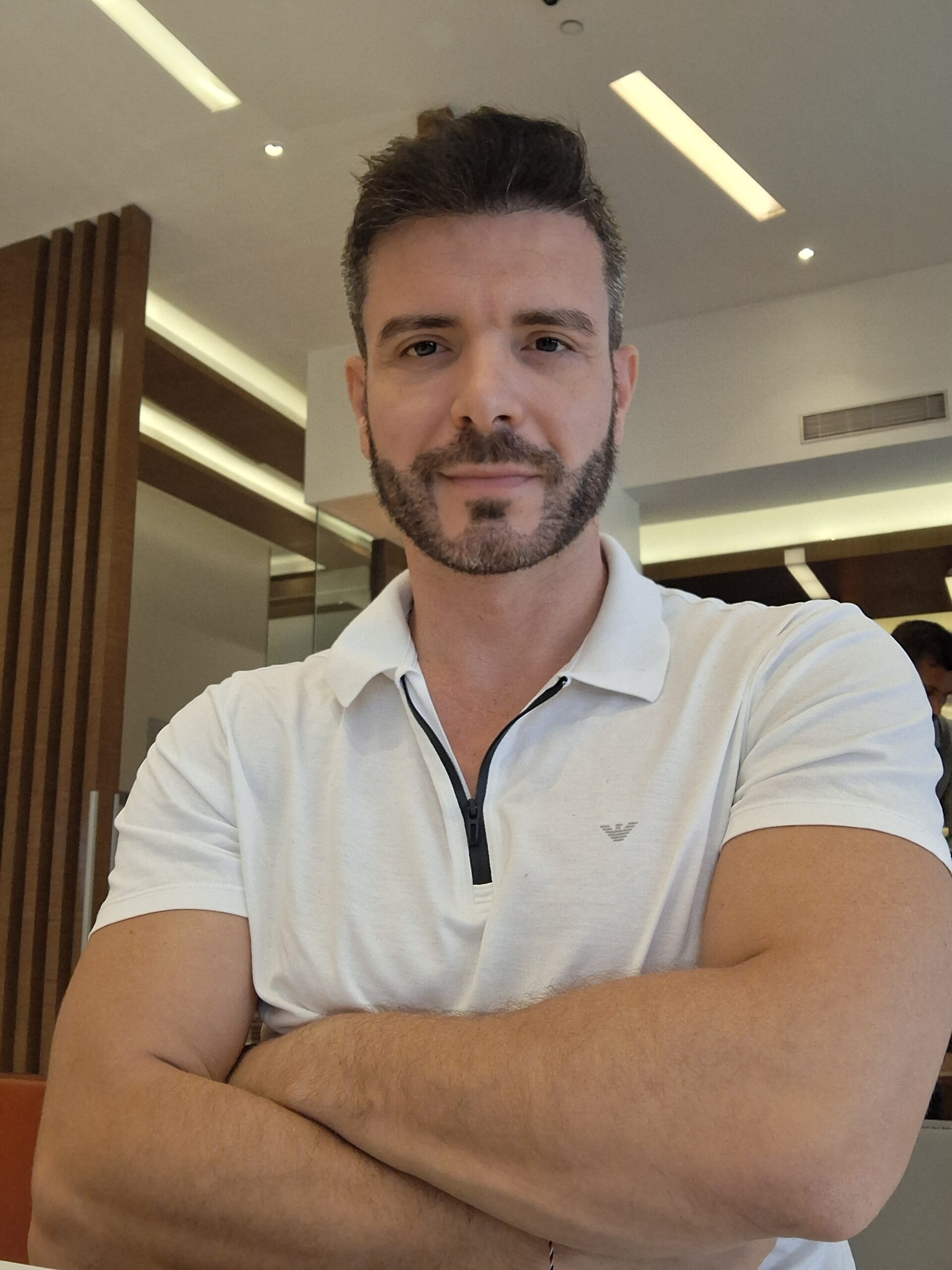
Helping businesses grow faster with AI. 🚀 At Callin.io, we make it easy for companies close more deals, engage customers more effectively, and scale their growth with smart AI voice assistants. Ready to transform your business with AI? 📅 Let’s talk!
Vincenzo Piccolo
Chief Executive Officer and Co Founder