Understanding the Foundations of Industry 4.0
The fourth industrial revolution, commonly known as Industry 4.0, represents a fundamental shift in how manufacturing operations are conducted. Unlike previous industrial revolutions that focused on mechanization, mass production, and basic automation, Industry 4.0 introduces cyber-physical systems that blur the lines between physical equipment and digital technology. At its core, Industry 4.0 leverages interconnected sensors, machines, and data systems to create smart factories capable of self-optimization and autonomous decision-making. According to a McKinsey report, companies implementing Industry 4.0 technologies have seen productivity improvements of 15-20%. The integration of artificial intelligence solutions forms the backbone of this transformation, enabling predictive capabilities and adaptive manufacturing environments that were previously unattainable. For businesses still exploring these concepts, conversational AI systems can provide an accessible entry point to understand how intelligent technologies can enhance operational processes.
The Role of AI in Driving Smart Manufacturing
AI solutions are not merely add-ons to Industry 4.0—they’re essential catalysts powering its core functionality. Smart manufacturing environments depend on AI algorithms to process vast amounts of sensor data, identify patterns, and make operational adjustments without human intervention. These systems transform traditional production lines into flexible, responsive environments that can adapt to changing market conditions. For example, machine learning models trained on historical production data can anticipate equipment failures before they occur, reducing downtime by up to 50% according to research from the World Economic Forum. AI-powered quality control systems using computer vision can inspect products 10 times faster than manual methods while detecting defects invisible to the human eye. AI voice agents, like those offered through Callin.io’s AI voice agent services, can maintain constant communication between different production units, ensuring smooth coordination without requiring staff to leave their stations.
Predictive Maintenance: Preventing Failures Before They Happen
One of the most impactful applications of AI in Industry 4.0 is predictive maintenance—the ability to forecast equipment failures before they occur. Traditional maintenance approaches fall into two problematic categories: reactive (fixing machines after they break, causing costly downtime) or preventative (performing maintenance on fixed schedules, often wasting resources on unnecessary interventions). AI predictive systems analyze real-time data from equipment sensors to detect subtle changes in vibration patterns, temperature fluctuations, or energy consumption that indicate potential issues. A study by Deloitte found that predictive maintenance increases equipment uptime by 10-20%, reduces maintenance costs by 5-15%, and extends machinery lifespan by 20-40%. Companies implementing these solutions through platforms such as AI call center technologies can establish automated alert systems that notify maintenance teams the moment anomalies are detected, prioritizing issues based on urgency and potential impact.
AI-Driven Quality Control and Inspection
Quality assurance represents another crucial area where AI technologies are revolutionizing Industry 4.0 operations. Automated inspection systems equipped with computer vision algorithms can examine products at speeds and accuracy levels unattainable by human inspectors. These systems utilize deep learning models trained on thousands of images of both defective and non-defective products to identify even microscopic flaws. For example, in semiconductor manufacturing, AI quality control systems can detect defects as small as 10 nanometers—about 10,000 times thinner than a human hair. According to research from Aberdeen Group, manufacturers implementing AI quality control systems have reduced defect rates by an average of 45%. These technologies are being integrated with conversational AI platforms to create systems that not only detect issues but can also communicate findings to relevant departments and automatically adjust production parameters to address recurring quality problems.
Supply Chain Optimization Through AI Analytics
Industry 4.0’s impact extends beyond factory walls into the entire supply chain ecosystem. AI-powered supply chain management tools analyze historical data, current market conditions, and real-time logistics information to optimize inventory levels, streamline distribution networks, and anticipate disruptions. These systems can reduce inventory costs by 15-30% while improving product availability by predicting demand fluctuations with unprecedented accuracy. During supply chain disruptions like those experienced during the COVID-19 pandemic, AI systems proved particularly valuable; companies using AI supply chain solutions were 65% more likely to avoid critical shortages, according to IBM research. Integration with AI calling solutions enables automated communication with suppliers and logistics partners, ensuring all stakeholders have current information and can respond quickly to changing conditions. This real-time coordination capability creates resilient supply networks that can withstand unexpected challenges while maintaining operational efficiency.
Digital Twins: Virtual Replicas for Real-World Optimization
Digital twin technology represents one of the most sophisticated applications of AI in Industry 4.0 environments. These virtual replicas of physical products, processes, or entire production facilities are continuously updated with real-world data, allowing engineers to test modifications and optimizations in the digital realm before implementing them in reality. According to Gartner, 13% of organizations implementing IoT projects already use digital twins, while 62% are either in the process of establishing digital twin use or plan to do so. The technology enables manufacturers to reduce development time by 20-50% while improving product performance. For example, General Electric uses digital twins to optimize wind turbine placement and operation, increasing energy production by up to 20%. These systems benefit from integration with AI voice conversation technologies that allow engineers to interact with digital models using natural language commands, making sophisticated simulation tools accessible to team members without specialized programming skills.
Autonomous Robots and Cobots in Smart Factories
The integration of autonomous robots and collaborative robots (cobots) represents a cornerstone of AI-enhanced Industry 4.0 implementations. Unlike traditional industrial robots that perform repetitive tasks within safety cages, modern AI-powered robots can navigate dynamic environments, recognize objects, and work alongside human employees. These systems learn from experience, continuously improving their performance through reinforcement learning techniques. According to the International Federation of Robotics, cobot installations are growing at a rate of 50% annually, far outpacing traditional robot deployment. These systems excel in tasks requiring precision and consistency, with error rates 70% lower than human operators for certain applications. Communication between robots and human team members is facilitated through AI call assistants that allow workers to redirect robot activities using simple voice commands, creating flexible production environments that combine the strengths of both human and machine intelligence.
Energy Optimization and Sustainable Manufacturing
AI solutions are driving significant improvements in energy efficiency and sustainability within Industry 4.0 facilities. Intelligent energy management systems monitor consumption patterns across manufacturing equipment, HVAC systems, and building infrastructure, automatically adjusting operations to minimize waste. These systems typically reduce energy consumption by 10-30% while maintaining or improving production output. By analyzing historical usage data and environmental conditions, AI algorithms can predict optimal production schedules that take advantage of lower-cost energy periods or reduced demand times. The World Economic Forum estimates that AI-enabled energy optimization could reduce global greenhouse gas emissions by 1.5-4% by 2030. Manufacturers implementing these technologies often coordinate their sustainability efforts using AI appointment schedulers to arrange regular efficiency reviews and track progress toward environmental goals, ensuring continuous improvement in resource utilization.
Customized Production and Mass Personalization
Industry 4.0 technologies powered by AI are enabling a shift from mass production to mass personalization—the ability to efficiently produce customized products at scale. Traditional manufacturing economics forced companies to choose between high-volume standardized products or low-volume custom items at premium prices. AI-driven production systems break this trade-off by optimizing equipment configurations, material flows, and quality protocols on the fly for each product variation. According to research from Deloitte, 36% of consumers express interest in personalized products or services, with 20% willing to pay a 20% premium. Companies implementing these capabilities have seen revenue increases of 5-10% and customer retention improvements of 25-30%. These custom production systems often utilize AI sales representatives to gather customer specifications and preferences, creating seamless transitions from order configuration to production scheduling without manual data re-entry or communication delays.
Augmented Reality and AI Vision Systems
The combination of augmented reality (AR) and AI creates powerful tools for worker assistance, quality verification, and training in Industry 4.0 environments. These systems overlay digital information onto the physical world, guiding employees through complex assembly procedures, maintenance tasks, or quality inspections. AI vision components analyze what the worker is seeing to identify parts, detect proper assembly, and flag potential errors. According to PTC research, industrial companies using AR-assisted work instructions report 30% faster task completion with 90% fewer errors. The technology is particularly valuable for training new employees, reducing training time by up to 60% while improving knowledge retention. These AR systems increasingly incorporate AI voice agents that respond to verbal queries, allowing workers to access information or request assistance without removing safety equipment or interrupting their workflow, further enhancing productivity and safety in manufacturing settings.
Cloud Computing and Edge AI for Industrial Applications
The infrastructure supporting Industry 4.0 AI applications relies on a strategic balance between cloud computing and edge AI processing. Cloud platforms provide the massive computational resources needed for training sophisticated AI models and analyzing enterprise-wide data, while edge devices enable real-time decision making without communication delays or connectivity concerns. This hybrid approach allows manufacturers to process time-sensitive data locally (like machine control signals) while sending aggregated information to the cloud for deeper analysis and global optimization. According to Gartner, by 2025, 75% of enterprise-generated data will be processed at the edge. Companies implementing this architecture typically achieve response times 10-100 times faster for critical applications while reducing bandwidth costs by 30-40%. Many manufacturers coordinate this distributed intelligence using AI phone services that provide centralized communication between cloud systems, edge devices, and human supervisors, ensuring consistent operation across the technology ecosystem.
Cybersecurity Challenges in Connected Manufacturing
The increased connectivity of Industry 4.0 systems creates new cybersecurity vulnerabilities that require AI-powered protection. Manufacturing facilities now contain thousands of networked sensors and control systems, each representing a potential entry point for cyber attacks. Traditional security approaches that rely on predefined threat signatures cannot keep pace with rapidly evolving attack methodologies. AI-based security systems analyze network traffic patterns, device behaviors, and user interactions to identify anomalies that may indicate compromise, even when the specific attack technique has never been seen before. According to the Manufacturing Leadership Council, 40% of manufacturing companies experienced a cybersecurity incident in the past year, with an average cost of $2.8 million per breach. Leading organizations are leveraging AI voice assistants for FAQ handling to provide security teams with immediate access to threat information and response protocols during potential incidents, reducing response times and minimizing impact.
Skills Development for the AI-Enhanced Factory
The transformation to AI-driven Industry 4.0 manufacturing requires significant workforce reskilling initiatives. While automation eliminates certain routine tasks, it creates demand for new roles focused on AI system management, data analysis, and cross-functional coordination. According to the World Economic Forum’s Future of Jobs Report, 50% of all employees will need reskilling by 2025 as technology adoption increases. Progressive manufacturers are implementing AI-guided learning programs that analyze each employee’s current skills, track their progress through training modules, and identify personalized development pathways. These systems typically improve skill acquisition rates by 25-30% compared to traditional training approaches. Many organizations utilize AI phone consultants for business to provide on-demand training support, allowing employees to verbalize questions or challenges and receive immediate guidance without disrupting production activities or waiting for instructor availability.
AI-Enabled Product Development and Innovation
Industry 4.0 extends AI’s impact beyond production efficiency into the realm of product development and innovation. Generative design systems use AI algorithms to explore thousands of possible design variations based on specified performance requirements, material constraints, and manufacturing methods. These systems typically identify solutions that are 20-30% lighter while maintaining or improving structural performance compared to traditional designs. AI analysis of customer feedback, warranty claims, and usage patterns helps identify improvement opportunities or unmet needs that drive product evolution. According to Boston Consulting Group, companies leveraging AI in product development reduce time-to-market by 30% and engineering hours by 25%. These design systems increasingly integrate with AI sales pitch generators to create compelling product presentations that accurately communicate the technical advantages and customer benefits of AI-optimized designs, ensuring marketing messages align with actual product capabilities.
Data Management Strategies for Industrial AI
Effective data management forms the foundation for successful AI implementation in Industry 4.0 environments. Manufacturing facilities generate enormous volumes of data—often terabytes daily from sensors, machines, quality systems, and operational databases. Converting this raw information into actionable intelligence requires sophisticated data processing pipelines that clean, normalize, and structure information for AI consumption. According to MIT Technology Review, organizations with mature data management practices are 2.5 times more likely to successfully implement AI projects. Leading manufacturers establish cross-functional data governance teams to define standards, ownership responsibilities, and quality metrics for their industrial datasets. They often leverage AI call center technologies to coordinate data-related issues between departments, ensuring that when anomalies or quality problems arise, the right stakeholders are automatically notified and can resolve issues before they impact AI system performance.
Return on Investment: Measuring AI Impact in Manufacturing
Quantifying the financial benefits of AI investments represents a critical challenge for Industry 4.0 adoption. Unlike traditional equipment purchases with straightforward productivity calculations, AI systems often deliver value through multiple channels simultaneously—reducing downtime, improving quality, decreasing energy consumption, and enabling new business capabilities. According to McKinsey, manufacturers implementing comprehensive AI strategies achieve EBITDA improvements of 10-15% within two to three years of deployment. Progressive organizations utilize balanced scorecard approaches that track both direct financial metrics and leading indicators like process stability, prediction accuracy, and decision speed. These measurement systems often connect to AI bot platforms that automatically generate performance reports and distribute them to stakeholders, ensuring consistent visibility into AI initiative outcomes and enabling rapid course correction when results deviate from expectations.
Integration Challenges: Connecting Legacy Systems with AI Solutions
The reality for most manufacturers is that Industry 4.0 AI implementations must work alongside legacy equipment and systems that were never designed for digital integration. This challenge requires specialized middleware and connectivity solutions that can extract data from older machines, translate proprietary protocols, and establish reliable communication pathways. Companies like Siemens have developed industrial IoT platforms specifically designed to bridge this gap between analog legacy systems and digital AI applications. According to research from PwC, manufacturers typically spend 40-60% of their Industry 4.0 budgets on integration and connectivity infrastructure. Organizations successfully navigating these challenges often utilize AI call assistants to coordinate between IT teams and operational technology specialists when integration issues arise, ensuring rapid problem resolution through clear communication across traditional departmental boundaries.
Ethical Considerations in Industrial AI Deployment
The implementation of AI systems in manufacturing environments raises important ethical considerations around worker displacement, data privacy, algorithmic transparency, and decision accountability. According to the AI Now Institute, organizations that proactively address these ethical dimensions experience 35% fewer implementation delays and higher rates of workforce acceptance. Progressive manufacturers establish clear policies regarding data collection from employees, transparency in how AI systems make recommendations, and processes for human oversight of autonomous decisions. They typically engage workers in the design and implementation of AI systems, viewing them as partners rather than subjects in the transformation process. Many organizations utilize AI voice conversation platforms to gather anonymous feedback from employees about their experiences with new technologies, creating safe channels for expressing concerns while identifying opportunities to improve both the technical and human aspects of AI deployment.
Global Industry 4.0 AI Adoption Trends
The implementation of AI-powered Industry 4.0 solutions varies significantly across regions, creating both challenges and opportunities for global manufacturers. According to the World Economic Forum, Asia leads in industrial robotics deployment with China alone accounting for 36% of global installations. European manufacturers tend to excel in sustainable manufacturing applications of AI, particularly energy optimization and circular economy solutions. North American companies typically show strength in software-intensive applications like predictive analytics and digital twins. This regional variation creates knowledge-sharing opportunities as best practices emerge from different industrial traditions. Global manufacturers increasingly rely on AI phone agents to facilitate cross-border collaboration, providing real-time translation and cultural context that enables teams to learn from international counterparts despite language differences and time zone challenges.
Future Directions: Quantum Computing and Next-Generation AI for Manufacturing
Looking ahead, the convergence of quantum computing and advanced AI promises to unlock capabilities far beyond today’s Industry 4.0 implementations. Quantum systems could solve complex optimization problems—like supply chain routing across thousands of locations or materials science simulations for new product development—that remain intractable for classical computers. According to IBM Research, quantum computing could potentially optimize manufacturing processes 100-1000 times more effectively than current methods once the technology matures. Similarly, next-generation AI systems utilizing few-shot learning and neuro-symbolic approaches may require far less training data while delivering more explainable results. Though these technologies remain developmental, forward-thinking manufacturers are establishing relationships with research institutions and technology providers to ensure early access to breakthrough capabilities. Many organize their exploration efforts using AI appointment schedulers to coordinate regular technology reviews with potential partners, systematically evaluating emerging solutions against their specific manufacturing challenges.
From Smart Factories to Intelligent Manufacturing Ecosystems
The future of Industry 4.0 extends beyond individual smart factories toward interconnected manufacturing ecosystems where AI coordinates production across multiple facilities, suppliers, and partners. These networks can dynamically reallocate production based on changing demand patterns, equipment availability, or supply disruptions. According to Accenture research, manufacturers operating in such collaborative networks achieve 15% higher profitability and 20% better capacity utilization than those managing facilities in isolation. These ecosystems enable advanced capabilities like distributed manufacturing, where products are produced closer to end customers by dynamically routing designs to the most appropriate facility. Organizations building these networks increasingly rely on white label AI receptionists to create consistent communication interfaces across ecosystem partners, ensuring smooth information flow despite differences in underlying systems and organizational structures.
Transforming Your Manufacturing Operation with AI Solutions
Implementing AI solutions for Industry 4.0 represents a journey rather than a destination. Successful transformations typically begin with clear problem identification—identifying specific operational challenges where AI can deliver meaningful impact. This targeted approach builds organizational confidence and demonstrates value before expanding to broader applications. According to Deloitte, manufacturers that follow this methodology are three times more likely to achieve positive ROI on their AI investments compared to those pursuing technology-first implementations. Start by establishing reliable data collection from critical equipment, then progress to basic analytics before implementing more sophisticated AI capabilities. Focus on building cross-functional teams that combine domain expertise with technical knowledge. Consider partnering with specialized AI service providers like those available through AI for call centers to accelerate your learning curve and access proven implementation methodologies that reduce risk and accelerate time-to-value.
Empowering Your Industry 4.0 Transformation with Intelligent Communication
When implementing AI solutions for Industry 4.0, effective communication becomes the critical thread connecting systems, departments, and partners. The most sophisticated manufacturing technologies deliver limited value if information can’t flow seamlessly between stakeholders. If you’re looking to enhance your manufacturing communication infrastructure to support your Industry 4.0 initiatives, consider exploring Callin.io. This platform allows you to deploy AI-powered phone agents that can coordinate between production teams, alert maintenance personnel when systems detect anomalies, and keep management informed of key performance metrics without requiring manual reporting.
Callin.io’s AI phone agents can interact naturally with your team members, understand manufacturing terminology, and ensure critical information reaches the right people at the right time. The free account provides an intuitive interface for configuring your AI agent, includes test calls, and offers access to the task dashboard for monitoring interactions. For manufacturers requiring advanced capabilities such as integration with production scheduling systems or CRM connectivity, subscription plans start at just $30 USD monthly. Discover how Callin.io can support your Industry 4.0 communication needs by visiting Callin.io today.
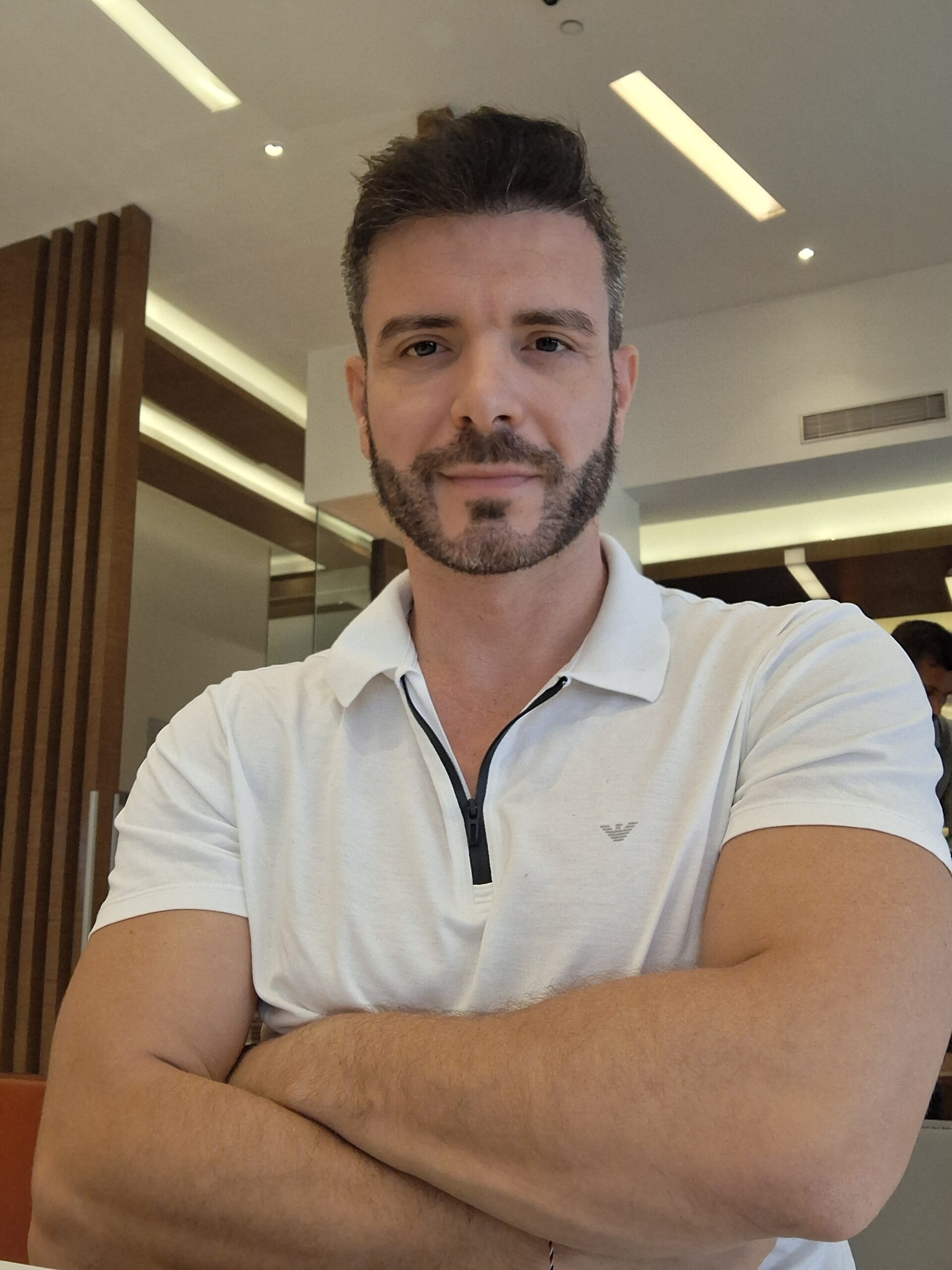
Helping businesses grow faster with AI. 🚀 At Callin.io, we make it easy for companies close more deals, engage customers more effectively, and scale their growth with smart AI voice assistants. Ready to transform your business with AI? 📅 Let’s talk!
Vincenzo Piccolo
Chief Executive Officer and Co Founder