Understanding the Foundation: What is Predictive Maintenance?
Predictive maintenance represents a groundbreaking shift from traditional reactive approaches to equipment care. Unlike conventional methods that wait for machinery breakdowns before taking action, predictive maintenance anticipates failures before they occur. This forward-thinking strategy leverages artificial intelligence to analyze operational data, identify patterns, and forecast potential issues with remarkable accuracy. By implementing AI solutions for predictive maintenance, companies can dramatically reduce unplanned downtime, extend equipment lifespan, and optimize maintenance schedules based on actual conditions rather than arbitrary timeframes. The core principle involves constant monitoring of machinery health through sensors and IoT devices that feed data into sophisticated AI algorithms. These systems continuously learn from historical performance data, becoming increasingly precise in their predictions over time. Organizations across manufacturing, energy, transportation, and utilities sectors have recognized that predictive maintenance represents a significant competitive advantage in today’s production-intensive industries, with the potential to slash maintenance costs by up to 30% according to industry research.
The Economic Impact of Maintenance Failures
The financial consequences of unexpected equipment failures extend far beyond immediate repair costs. When critical machinery breaks down without warning, businesses face a cascade of expenses: emergency repairs often come with premium pricing, production schedules get disrupted, delivery commitments are missed, and customer satisfaction plummets. In manufacturing environments, a single hour of unplanned downtime can cost anywhere from thousands to millions of dollars depending on the industry. According to a report by Aberdeen Group, unplanned downtime costs industrial manufacturers an estimated $50 billion annually. The ripple effects touch every aspect of business operations, from workforce management to supply chain integrity. AI-powered predictive maintenance directly addresses these economic vulnerabilities by minimizing surprise failures through early detection of developing problems. By transitioning from crisis management to strategic maintenance planning, companies can redirect resources toward growth initiatives rather than emergency responses. As noted in our analysis of AI for call centers, the same predictive capabilities that enhance customer service can be applied to machine performance, creating data-driven maintenance strategies that protect bottom-line profitability through operational reliability.
The Technology Stack Behind AI-Driven Maintenance
The technical architecture supporting predictive maintenance solutions combines multiple technologies working in harmony. At its foundation are industrial IoT sensors that collect real-time data on temperature, vibration, pressure, sound, and other operational parameters from equipment. This continuous stream of information travels through secure networking infrastructure to centralized or edge computing systems where the real analytical magic happens. Machine learning algorithms—particularly those focused on anomaly detection, regression analysis, and pattern recognition—form the intelligence core of the system. These algorithms process massive datasets to distinguish between normal operational variations and true warning signs of impending failure. Supporting this analytical engine are data management systems that handle the enormous volume of information generated by industrial equipment. Cloud platforms provide the scalable computing resources needed for complex calculations, while edge computing enables rapid response for time-sensitive applications. The integration of conversational AI capabilities allows maintenance teams to interact with these systems through natural language interfaces, making sophisticated technology accessible to frontline workers without requiring specialized technical knowledge.
Key Machine Learning Models Powering Predictive Insights
The intelligence behind effective predictive maintenance lies in specialized machine learning models tailored to equipment monitoring challenges. Supervised learning algorithms excel at failure prediction when historical data includes labeled examples of previous breakdowns, allowing the system to recognize similar patterns as they develop. For detecting unusual operating conditions without prior examples, unsupervised learning models apply clustering and anomaly detection techniques to identify deviations from normal performance profiles. Deep learning neural networks have proven particularly valuable for processing complex sensor data like vibration signatures or acoustic emissions that contain subtle indicators of developing problems. Time series analysis models track performance trends over extended periods, distinguishing between seasonal variations and genuine deterioration. For equipment with multiple potential failure modes, ensemble methods combine predictions from several algorithms to improve overall accuracy. The sophistication of these approaches continues to advance, with models now capable of identifying not just that a failure might occur, but specifically which component is at risk and the likely timeframe for failure. Companies implementing AI call assistants are finding similar pattern recognition benefits in both customer interactions and equipment monitoring, demonstrating the versatility of these analytical approaches across business operations.
Implementation Roadmap: From Data Collection to Actionable Insights
Deploying AI predictive maintenance involves a structured journey that begins with a comprehensive assessment of current maintenance challenges and critical equipment. The initial phase focuses on sensor deployment and connectivity, ensuring the right data streams are available for analysis. Organizations should prioritize equipment based on operational impact and failure costs, starting with high-value assets. The second phase centers on data infrastructure development, establishing the pipelines, storage solutions, and processing capabilities needed to handle industrial data volumes. During the third phase, maintenance teams collaborate with data scientists to develop and train the predictive models, incorporating domain expertise into algorithmic design. The fourth phase involves integration with existing maintenance management systems and workflow tools to ensure insights translate into action. Finally, organizations must establish continuous improvement processes to refine models based on real-world outcomes. Companies like Callin.io have demonstrated how similar implementation approaches for AI communication technologies can provide a template for successful deployment of predictive maintenance solutions, emphasizing the importance of strategic planning, stakeholder involvement, and iterative refinement.
IoT Sensors: The Eyes and Ears of Predictive Systems
The foundation of any predictive maintenance program lies in comprehensive data collection through strategically placed sensors. These sophisticated IoT monitoring devices serve as the sensory system for industrial equipment, capturing vital signs that reveal internal conditions. Modern predictive maintenance deployments typically utilize multiple sensor types, including vibration analyzers that detect subtle changes in equipment oscillation patterns, thermal imaging sensors that identify hotspots indicating friction or electrical issues, acoustic monitors that recognize changes in operational sounds, pressure sensors that track fluid system health, and electrical consumption meters that spot efficiency losses. The latest generation of industrial sensors features impressive capabilities: miniaturization allows placement in previously inaccessible locations, energy harvesting technologies enable wireless operation without battery replacement, and edge processing capabilities allow preliminary analysis directly at the sensor level. The integration challenges involve determining optimal sensor placement, establishing reliable connectivity in challenging industrial environments, and managing the substantial data volumes generated. Organizations implementing IoT sensor networks should consider consulting AI voice agent specialists who understand the parallels between speech processing and industrial signal analysis, as both domains involve extracting meaningful patterns from complex waveforms.
Real-Time Monitoring: Transforming Data Streams into Operational Intelligence
The continuous flow of sensor data becomes truly valuable when transformed into real-time operational intelligence accessible to decision-makers. Advanced monitoring dashboards represent the interface between complex analytical systems and human operators, providing visual representations of equipment health that highlight emerging concerns requiring attention. These interfaces prioritize exceptional clarity, using color-coded status indicators, trend visualizations, and contextual alerts to communicate equipment condition at a glance. The most effective systems incorporate configurable thresholds allowing maintenance teams to adjust sensitivity based on operational priorities and risk tolerance. Modern dashboards integrate both historical performance data and forward-looking predictive elements, enabling side-by-side comparison of current conditions against expected baselines. Mobile accessibility ensures critical alerts reach appropriate personnel regardless of location, while integration with AI appointment scheduling systems can automatically reserve maintenance resources when potential issues are detected. The real-time monitoring layer should provide appropriate information granularity for different organizational roles—overview perspectives for management, detailed diagnostic data for specialists, and actionable alerts for frontline responders—ensuring everyone has the right information to fulfill their responsibilities in maintaining operational reliability.
Case Study: Manufacturing Sector Transformation Through Predictive Maintenance
A leading automotive parts manufacturer provides a compelling illustration of predictive maintenance impact at scale. Facing increasing pressure to improve production reliability while reducing maintenance costs, the company implemented an AI-driven predictive system across its production facilities. The implementation focused initially on critical forming presses where unexpected failures resulted in substantial production losses. Vibration analysis algorithms proved particularly effective, detecting subtle changes in press operation weeks before visible symptoms appeared. Within the first year of deployment, the manufacturer documented a 62% reduction in unplanned downtime for monitored equipment, with maintenance costs decreasing by 28% as emergency repairs gave way to planned interventions. The predictive insights transformed maintenance scheduling, allowing the company to consolidate previously scattered maintenance activities into coordinated efforts that minimized production disruption. The success expanded beyond direct maintenance benefits, as improved equipment reliability enabled more precise production planning and inventory management. The company integrated its predictive maintenance platform with its customer service systems, allowing sales teams to make more reliable delivery commitments based on improved operational stability. This manufacturing transformation illustrates how predictive maintenance delivers multifaceted business benefits extending far beyond the maintenance department, becoming a strategic competitive advantage in reliability-sensitive industries.
Energy Sector Applications: Maximizing Uptime in Critical Infrastructure
The energy generation and distribution sector has emerged as a leading adopter of AI predictive maintenance due to the catastrophic consequences of equipment failures. Power generation facilities utilize sophisticated condition monitoring systems on critical assets like turbines, generators, transformers, and pumping systems. Wind farm operators, for instance, have deployed machine learning models that analyze vibration signatures from gearboxes and bearings, predicting component failures up to six months in advance and scheduling repairs during low-wind periods to minimize revenue impact. Utility companies responsible for transmission and distribution infrastructure leverage drone-captured imagery processed by computer vision algorithms to detect early signs of insulator deterioration or vegetation encroachment. The predictive maintenance approach has proven particularly valuable for remote assets spread across vast geographical areas, where physical inspections are costly and time-consuming. Nuclear facilities utilize advanced predictive technologies to maintain exceptional reliability standards while optimizing maintenance activities within strict regulatory frameworks. The energy sector’s experience demonstrates how predictive maintenance not only prevents costly failures but also contributes to energy security through improved infrastructure reliability. Companies providing AI voice conversation tools have found productive applications in energy facility control rooms, where natural language interfaces simplify access to complex predictive maintenance insights during operational decision-making.
Transportation and Logistics: Keeping the Supply Chain Moving
The transportation sector faces unique maintenance challenges with assets continually in motion across diverse environments. Airlines have pioneered advanced predictive maintenance programs that analyze engine data, flight parameters, and environmental conditions to anticipate component needs before aircraft return to maintenance bases. These systems have reduced flight delays attributable to mechanical issues by up to 30% for early adopters. In the rail industry, intelligent monitoring systems installed along tracks and on rolling stock detect developing wheel defects, bearing problems, and track anomalies, preventing derailments through timely intervention. Commercial fleet operators implement vehicle telemetry systems that combine engine performance data, driver behavior metrics, and environmental factors to optimize maintenance schedules for each vehicle’s specific usage pattern. Maritime shipping companies deploy hull-mounted sensors and propulsion monitoring systems that adjust maintenance requirements based on actual operating conditions rather than arbitrary schedules. The transportation sector’s implementations demonstrate how predictive maintenance directly impacts customer experience, with improved reliability translating to consistent delivery timing and reduced delays. The integration of predictive systems with AI phone services allows transportation companies to proactively communicate with customers about potential schedule adjustments when maintenance needs are detected, maintaining service quality even when interventions are necessary.
Healthcare Infrastructure: Ensuring Uninterrupted Patient Care
Healthcare facilities maintain complex equipment portfolios where reliability directly impacts patient outcomes. Hospitals implement medical equipment monitoring systems that track the performance of critical assets like MRI machines, ventilators, and laboratory equipment. Advanced predictive algorithms analyze subtle changes in operational parameters to identify developing issues before they affect clinical usage. The healthcare applications extend beyond diagnostic equipment to building infrastructure systems critical for patient safety, including backup power generators, medical gas distribution networks, and HVAC systems maintaining sterile environments. Biomedical engineering teams leverage predictive insights to schedule maintenance activities during periods of lowest clinical demand, minimizing disruption to patient care. The economic impact is substantial—preventing an MRI machine failure through predictive maintenance can save a healthcare facility over $100,000 in emergency repair costs and lost revenue, while ensuring critical diagnostic services remain continuously available. The integration with AI appointment scheduling systems allows maintenance to be coordinated with clinical schedules, maintaining healthcare operational continuity. The healthcare sector’s experience demonstrates how predictive maintenance contributes to both operational efficiency and quality of care by ensuring the reliability of life-critical equipment and infrastructure systems.
Building Management Systems: Smart Infrastructure Maintenance
Commercial and institutional buildings represent complex ecosystems of interdependent systems where predictive maintenance delivers significant operational benefits. Modern buildings equipped with intelligent monitoring infrastructure collect data from HVAC equipment, elevators, electrical distribution systems, and plumbing networks to maintain optimal environmental conditions while minimizing energy consumption and maintenance requirements. Machine learning algorithms analyze patterns in system performance to identify inefficiencies and developing problems, such as chillers consuming excessive electricity due to scaling buildup or air handlers showing early signs of bearing wear. The predictive approach has proven particularly valuable for optimizing maintenance resources across large property portfolios, allowing facility management teams to address developing issues before they escalate into tenant-impacting failures. Predictive algorithms also support sustainability goals by ensuring building systems operate at peak efficiency, reducing energy consumption while extending equipment lifespan. The building management applications demonstrate how predictive maintenance addresses both technical reliability and occupant experience considerations. Integration with AI phone agents allows property management teams to preemptively communicate with tenants about planned maintenance activities identified through predictive analysis, maintaining service transparency while addressing developing issues.
ROI Calculation: Making the Business Case for Predictive Maintenance
The financial justification for predictive maintenance investments requires comprehensive analysis of both direct cost savings and operational benefits. The most compelling ROI calculations include multiple value streams: reduced emergency repair expenses (typically 50-80% higher than planned maintenance), decreased spare parts inventory requirements through just-in-time ordering, extended equipment lifespan from optimized operating conditions, lower energy consumption through maintained efficiency, and increased production capacity from improved uptime. Organizations should establish baseline metrics before implementation, including current maintenance costs, downtime frequency, repair expenses, and production impacts. Industry benchmarks suggest mature predictive maintenance programs deliver 25-30% cost reduction, 70-75% decrease in breakdowns, and 35-45% reduction in downtime. Initial implementation costs typically include sensor infrastructure, connectivity, software platforms, integration services, and team training. The payback period varies by industry and application, ranging from 3-18 months, with critical production environments seeing the fastest returns. When calculating ROI, companies should include both quantifiable benefits and qualitative improvements to operational stability and planning capabilities. The analytical approach parallels ROI assessment for AI sales tools, where both direct cost savings and revenue enhancement opportunities factor into investment justification.
Overcoming Implementation Challenges: Practical Considerations
Organizations implementing predictive maintenance solutions should anticipate several common challenges that can affect project success. Data quality issues frequently emerge as a primary challenge—historical maintenance records may be inconsistent or incomplete, sensor data might contain gaps or inaccuracies, and operational context information could be missing. Successful implementations address these challenges through rigorous data validation processes and supplementary data collection where necessary. Integration with existing enterprise systems presents another hurdle, as predictive maintenance platforms must exchange information with maintenance management software, inventory systems, and production planning tools. Technical skills gaps within existing maintenance teams can slow adoption, requiring targeted training programs focused on both analytical understanding and practical application of predictive insights. Change management considerations are equally important, as shifting from reactive to predictive approaches requires adjustments to established maintenance workflows and resource allocation processes. Organizations should develop implementation strategies that address these challenges through phased deployments, focused training, and clear communication about the transition process. Companies exploring AI call center implementation face similar organizational adoption challenges and can apply comparable change management strategies to ensure successful technological transformation.
Human-AI Collaboration: The Evolving Role of Maintenance Professionals
Rather than replacing maintenance professionals, predictive maintenance technology transforms their roles into more strategic positions. Successful implementations establish effective collaboration models where AI systems handle data analysis and pattern recognition while human experts contribute contextual understanding, decision-making, and hands-on intervention. Maintenance technicians evolve from reactive troubleshooters to proactive reliability specialists who interpret AI-generated insights, prioritize response actions, and apply their experience to complex situations where algorithmic recommendations require adaptation. The shift necessitates new skill development in data interpretation, system configuration, and root cause analysis. Organizations should invest in comprehensive training programs that build both technical knowledge and confidence in working with AI recommendations. The most effective implementations recognize the complementary strengths of human and artificial intelligence: AI excels at consistent analysis of massive datasets to identify subtle patterns, while human experts excel at understanding operational context, adapting to unusual circumstances, and applying mechanical expertise during interventions. This collaborative approach mirrors developments in AI voice assistants where technology handles routine interactions while human specialists address complex situations requiring judgment and empathy.
Predictive Maintenance for Small and Medium Enterprises
While large industrial organizations pioneered predictive maintenance adoption, technological advancements have made these capabilities increasingly accessible to smaller operations. Cost-effective solutions now provide SMEs with predictive capabilities through several implementation approaches: cloud-based platforms that eliminate the need for extensive on-premises infrastructure, scalable sensor technologies that allow gradual deployment focused on critical equipment, and industry-specific pre-configured solutions that reduce implementation complexity. Small manufacturers can begin with targeted applications addressing their most unreliable or critical equipment, achieving meaningful improvements without enterprise-scale investments. Modular platforms allow progressive expansion as initial implementations demonstrate value. Collaborative approaches have emerged in some industries, where equipment vendors provide predictive maintenance as a value-added service or regional industry clusters share implementation resources. SMEs should focus initial efforts on applications with clear, short-term payback potential, such as historically problematic equipment or production bottlenecks where reliability directly impacts revenue. The democratization of predictive maintenance parallels developments in AI communication tools like AI receptionists that bring enterprise-grade capabilities to smaller organizations through accessible service models requiring minimal upfront investment.
Security Considerations for Connected Industrial Systems
The integration of sensors, networks, and cloud analytics into industrial environments introduces important security considerations that must be addressed as part of any predictive maintenance implementation. Industrial cybersecurity protocols should include several critical elements: secure-by-design sensor networks with encrypted communications, robust authentication mechanisms for all system access points, network segmentation that isolates operational technology from general IT infrastructure, regular security audits and vulnerability assessments, and comprehensive incident response planning. Organizations must consider both data security (protecting sensitive operational information) and operational security (preventing unauthorized system control). The security framework should address the entire data lifecycle from collection through processing, storage, and eventual archiving or deletion. Regulatory compliance requirements vary by industry, with critical infrastructure sectors facing particularly stringent oversight. As predictive maintenance systems increasingly connect to other enterprise applications, comprehensive security governance becomes essential to maintain appropriate access controls and data handling practices. The security considerations mirror those facing conversational AI for medical offices, where protecting sensitive information while maintaining operational functionality requires balanced, multi-layered security approaches.
Future Directions: The Evolution of Predictive Technologies
The predictive maintenance landscape continues to advance rapidly, with several emerging technologies poised to deliver even greater capabilities. Digital twin technology represents a significant frontier, creating comprehensive virtual replicas of physical assets that simulate performance under various conditions and predict future states with unprecedented accuracy. Augmented reality interfaces are transforming how maintenance teams interact with predictive insights, overlaying diagnostic information and repair guidance directly onto equipment within the technician’s field of view. Advanced sensor technologies, including non-contact monitoring methods and self-powering IoT devices, are expanding the range of equipment that can be effectively monitored. Quantum computing developments promise to revolutionize pattern recognition capabilities for complex industrial systems, identifying subtle interactions between variables that current computing approaches cannot detect. Edge computing architectures are enabling real-time analysis even in remote locations with limited connectivity. Perhaps most significantly, predictive maintenance is evolving beyond individual asset monitoring toward holistic production system optimization, where AI analyzes interactions between connected equipment to maintain optimal overall system performance. Organizations implementing today’s solutions should consider architectural approaches that can accommodate these emerging capabilities, similar to how AI caller platforms are designed with extensibility to incorporate future communication technologies.
Industry Standards and Best Practices
The maturing predictive maintenance field has developed frameworks and standards to guide implementation and operation. Organizations should familiarize themselves with relevant industry guidelines including ISO 55000 (asset management standards providing overall framework for maintenance programs), ISO 13374 (standards specific to condition monitoring and diagnostics), and industry-specific frameworks like the API 581 for risk-based inspection in petrochemical applications. Implementation best practices include establishing clear reliability objectives aligned with business goals, developing comprehensive data governance policies, implementing layered analytical approaches combining multiple techniques, creating standardized workflows for addressing predictive alerts, and establishing continuous improvement processes to refine models based on outcomes. Organizations should plan for appropriate staffing models that balance centralized analytical expertise with distributed operational knowledge. Knowledge-sharing mechanisms, including documentation of failure patterns and intervention effectiveness, help build organizational learning capacity. Regular assessment against maturity models allows organizations to benchmark their implementation and identify advancement opportunities. These structured approaches provide implementation guidance similar to the frameworks recommended for AI customer service deployment, where standardized processes ensure consistent quality while accommodating operational variations.
Case Study: Utility Company Transforms Maintenance Operations
A regional power utility demonstrates the transformative potential of comprehensive predictive maintenance implementation. Facing aging infrastructure and increasing reliability demands, the company deployed an integrated monitoring system across its generation facilities and distribution network. The implementation included turbine vibration analysis at generating stations, transformer oil composition monitoring for substation equipment, and drone-based infrared inspection of transmission lines. The utility established a centralized reliability center where specialists analyze incoming data and coordinate with field teams executing maintenance activities. Within three years of implementation, the utility documented 43% reduction in unplanned outages, 58% decrease in emergency maintenance costs, and 22% improvement in overall maintenance efficiency. The predictive capabilities enabled more precise workforce planning, with scheduled activities replacing emergency responses and improving both cost efficiency and worker safety. Perhaps most significantly, the improved reliability metrics translated directly to regulatory compliance and customer satisfaction benefits. The utility’s approach included extensive integration between its predictive maintenance systems and customer communication platforms, including AI phone assistance that provided automated updates during maintenance activities affecting service areas. This comprehensive case demonstrates how predictive maintenance delivers multifaceted benefits across technical, operational, regulatory, and customer experience dimensions.
Implementing Predictive Maintenance: Your Next Steps
Organizations ready to explore predictive maintenance should begin with a structured assessment and planning process. Start by conducting a criticality analysis of your equipment portfolio, identifying assets where improved reliability would deliver the greatest operational benefit. Evaluate your current data collection capabilities, including existing sensors, historian systems, and maintenance records that could support initial predictive modeling. Develop clear objectives aligned with business priorities, whether focused on cost reduction, uptime improvement, or regulatory compliance. Consider beginning with a pilot implementation on selected high-value equipment to demonstrate concept viability and refine your approach before broader deployment. Assess potential technology partners based on industry experience, integration capabilities, and alignment with your specific operational requirements. Develop internal expertise through targeted training programs that prepare your team to effectively interpret and act on predictive insights. Establish clear metrics to measure implementation success, including both technical performance indicators and business impact measurements. Organizations following this structured approach typically achieve faster implementation timeframes and stronger operational results than those pursuing ad-hoc deployments. For assistance with the technological aspects of industrial automation, consider AI integration specialists who understand the parallels between customer communication systems and industrial monitoring platforms.
Transforming Maintenance Operations: Take Action Today with Callin.io
The journey toward AI-powered predictive maintenance represents a fundamental shift in how organizations approach equipment reliability and operational excellence. This transition from reactive to predictive approaches delivers compelling benefits across cost reduction, production reliability, and asset longevity dimensions. Companies achieving the greatest success recognize that implementation involves not just technological deployment but organizational transformation in how maintenance activities are planned, prioritized, and executed based on data-driven insights. The predictive approach aligns maintenance resources with actual equipment needs rather than calendar-based schedules, optimizing both maintenance effectiveness and resource utilization.
If you’re looking to bring similar efficiency and intelligence to your business communications, Callin.io offers powerful solutions worth exploring. Our platform enables AI-powered phone agents that can autonomously handle incoming and outgoing calls with remarkable natural conversation capabilities. From booking appointments to answering frequent questions and even closing sales, our AI voice technology streamlines communication processes just as predictive maintenance optimizes equipment reliability.
Callin.io offers a free account with an intuitive interface for configuring your AI agent, including test calls and a comprehensive task dashboard for monitoring interactions. For businesses requiring advanced capabilities like Google Calendar integration and built-in CRM functionality, subscription plans start at just $30 monthly. Discover how Callin.io can transform your business communications with the same data-driven intelligence that predictive maintenance brings to industrial operations.
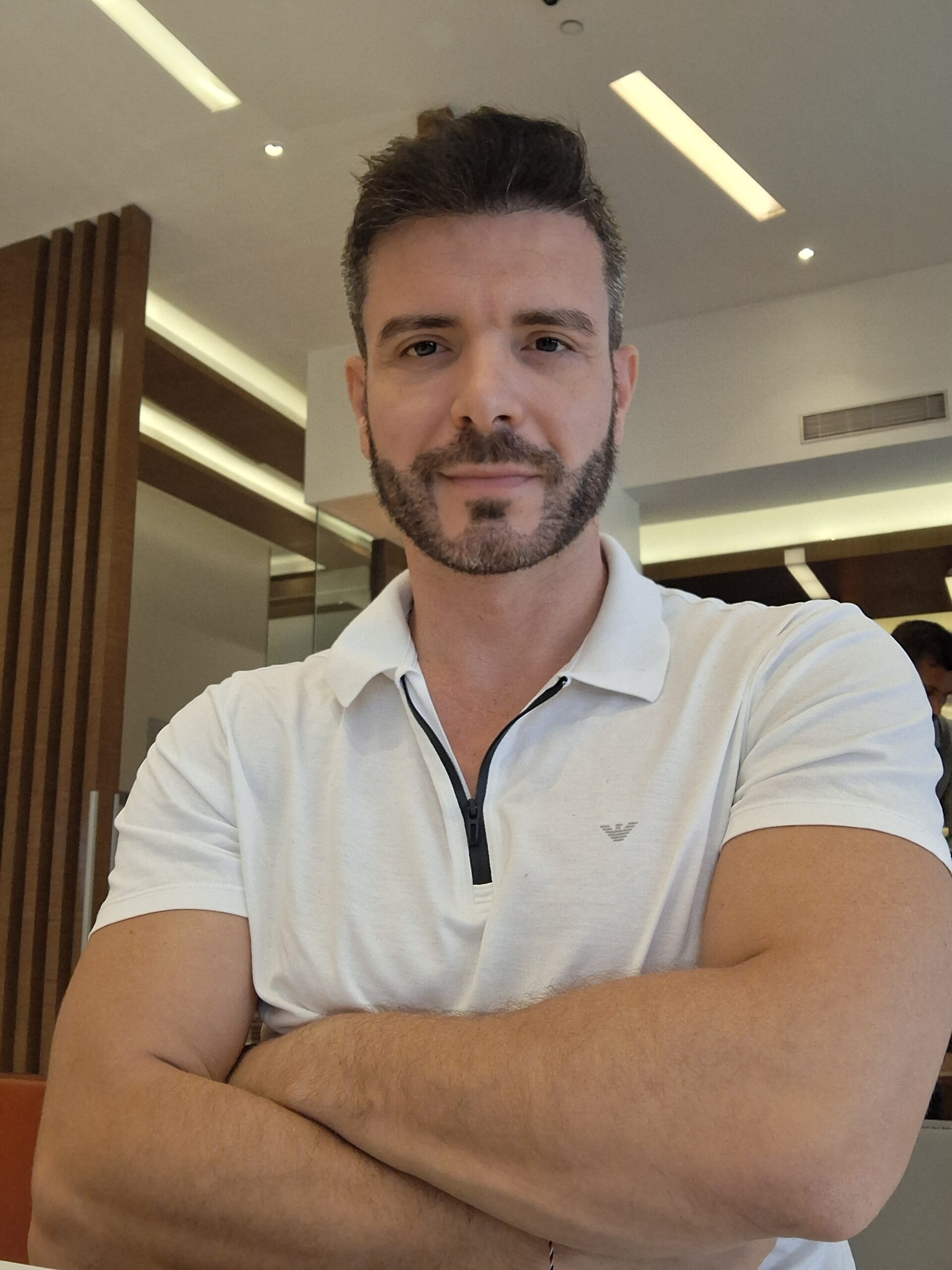
Helping businesses grow faster with AI. 🚀 At Callin.io, we make it easy for companies close more deals, engage customers more effectively, and scale their growth with smart AI voice assistants. Ready to transform your business with AI? 📅 Let’s talk!
Vincenzo Piccolo
Chief Executive Officer and Co Founder